Copper wire drawing process
A wire drawing and process technology, which is applied in the field of copper wire drawing process, can solve problems such as low production efficiency, dust and noise pollution, and high labor intensity, and achieve the effects of improving the pass rate, saving electric energy, and improving annealing quality
- Summary
- Abstract
- Description
- Claims
- Application Information
AI Technical Summary
Problems solved by technology
Method used
Image
Examples
Embodiment Construction
[0020] The specific content of the present invention will be described in detail below in conjunction with the accompanying drawings and specific embodiments.
[0021] A copper wire drawing process, including alkaline electrolysis, cleaning, oxygen content measurement, wire drawing, annealing, winding, inspection,
[0022] Electrolyze the copper rod in an alkaline solution containing 100-150g / L sodium hydroxide and 20-30g / L sodium tartrate to remove the copper oxide film; clean it after reaching the specified time, dry it and then pass the pulse melting infrared absorption Determination of the oxygen content of the copper rod after removing the oxide film, when the oxygen content is lower than 6000PPM, it can be used.
[0023] The wire drawing adopts a large drawing machine, a medium drawing machine, and a micro drawing machine. The large drawing machine and the medium drawing machine are respectively annealed after drawing. The large drawing machine stretches the diameter of ...
PUM
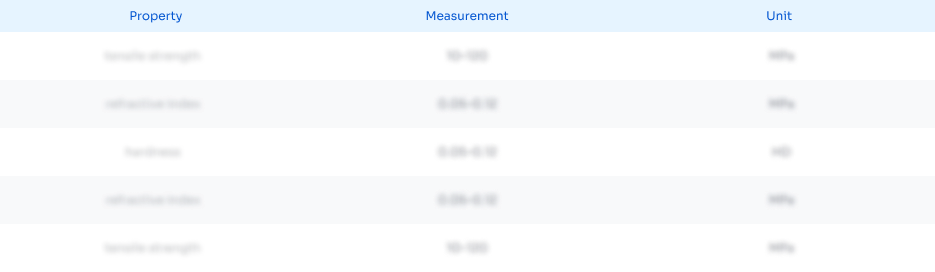
Abstract
Description
Claims
Application Information

- R&D Engineer
- R&D Manager
- IP Professional
- Industry Leading Data Capabilities
- Powerful AI technology
- Patent DNA Extraction
Browse by: Latest US Patents, China's latest patents, Technical Efficacy Thesaurus, Application Domain, Technology Topic, Popular Technical Reports.
© 2024 PatSnap. All rights reserved.Legal|Privacy policy|Modern Slavery Act Transparency Statement|Sitemap|About US| Contact US: help@patsnap.com