Preparation method of dicyclohexylcarbodiimide
A technology of dicyclohexylcarbodiimide and dicyclohexylurea, which is applied in the field of organic compound synthesis, can solve environmental pollution and other problems, and achieve the effect of simple process
- Summary
- Abstract
- Description
- Claims
- Application Information
AI Technical Summary
Problems solved by technology
Method used
Examples
Embodiment 1
[0020] Add 100g of dicyclohexyl urea to a mixed system consisting of 200mL of water and 200mL of methyl tert-butyl ether, stir and wash for 30min, filter it with suction, and dry it in a vacuum oven at 50°C until constant weight.
[0021] Put 50 g of dicyclohexyl urea and 300 mL of methyl tert-butyl ether into a dry three-necked flask, and stir evenly. At 25-35°C, add 42.5g of oxalyl chloride solution dropwise to the three-necked flask, control the dropping time to 3h, and the dropping temperature to , and keep warm for 0.5h after the dropping is completed. Take 26.8g of sodium hydroxide and make 15% lye. At 40-45°C, add the reaction solution dropwise to the alkaline solution, and control the dropping time to 6h. Then suction filtration, after the filtrate is layered, the organic phase is obtained, the solvent is removed by normal pressure distillation, and then vacuum distillation is carried out under the pressure of 1.35-1.54KPa, the fraction at 153-156°C is collected, and ...
Embodiment 2
[0023] Add 100g of dicyclohexyl urea into a mixed system consisting of 200mL of water and 200mL of dichloromethane and stir for 30min, filter it with suction and dry it in a vacuum oven at 50°C until it reaches a constant weight.
[0024] Put 50g of dicyclohexylurea and 400mL of dichloromethane into a dry three-necked flask, and stir evenly. At 10-20°C, add 31g of oxalyl chloride solution dropwise to the three-necked flask, control the dropping time to 4h, and the dropping temperature to , and keep warm for 0.5h after the dropping is completed. Take 20g of sodium hydroxide and make 15% lye. At 25-30°C, add the reaction solution dropwise to the alkali solution, and control the dropping time to 8h. Then suction filtration, the filtrate was distilled under normal pressure to remove the solvent, and then distilled under reduced pressure at a pressure of 1.35-1.54KPa to collect fractions at 153-156°C and vacuum-dried to obtain the product with a purity of 96.7% and a yield of 87.3...
Embodiment 3
[0026] Add 100g of dicyclohexyl urea into a mixed system consisting of 200mL of water and 200mL of methyl tetrahydrofuran, stir and wash for 30min, filter it with suction, and dry it in a vacuum oven at 50°C until constant weight.
[0027] Put 50 g of dicyclohexyl urea and 300 mL of methyl tetrahydrofuran into a dry three-necked flask, and stir evenly. At 25-35°C, add 31g of oxalyl chloride solution dropwise to the three-necked flask, control the dropping time to 1.5h, and the dropping temperature to , and keep warm for 0.5h after the dropping is completed. Take 20g of sodium hydroxide and make 15% lye. At 40-45°C, add the reaction solution dropwise to the alkaline solution, and control the dropping time to 4h. Then suction filtration, the filtrate was distilled under normal pressure to remove the solvent, and then distilled under reduced pressure at a pressure of 1.35-1.54KPa to collect fractions at 153-156°C and vacuum-dried to obtain the product with a purity of 95.2% and ...
PUM
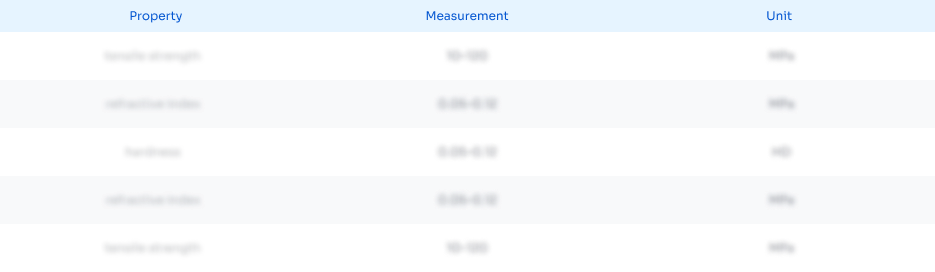
Abstract
Description
Claims
Application Information

- Generate Ideas
- Intellectual Property
- Life Sciences
- Materials
- Tech Scout
- Unparalleled Data Quality
- Higher Quality Content
- 60% Fewer Hallucinations
Browse by: Latest US Patents, China's latest patents, Technical Efficacy Thesaurus, Application Domain, Technology Topic, Popular Technical Reports.
© 2025 PatSnap. All rights reserved.Legal|Privacy policy|Modern Slavery Act Transparency Statement|Sitemap|About US| Contact US: help@patsnap.com