Dust-free microwave vacuum drying device for optical lens resin raw material
A technology of microwave vacuum drying and resin raw materials, which is applied in the direction of drying gas arrangement, heating device, drying solid materials, etc., which can solve the problems of increasing the difficulty of guaranteeing the operation of the purification system, the inability to completely remove dust, and waste of raw materials.
- Summary
- Abstract
- Description
- Claims
- Application Information
AI Technical Summary
Problems solved by technology
Method used
Image
Examples
Embodiment Construction
[0036] The implementation mode of the present invention is illustrated by specific specific examples below, and those who are familiar with this technology can easily understand other advantages and effects of the present invention from the contents disclosed in this description. Obviously, the described embodiments are a part of the present invention. , but not all examples. Based on the embodiments of the present invention, all other embodiments obtained by persons of ordinary skill in the art without making creative efforts belong to the protection scope of the present invention.
[0037] In order to solve the relevant technical problems existing in the prior art, the embodiment of the present application provides a dust-free microwave vacuum drying device for optical lens resin raw materials, which is mainly used for dust removal and drying of plastic optical resin injection molding raw material products for processing mobile phone optical lenses. dry. It includes a contr...
PUM
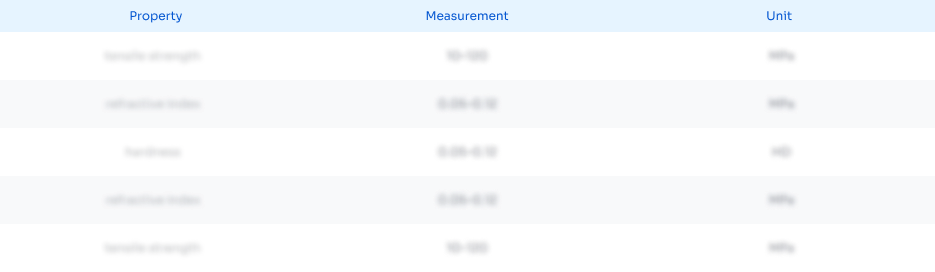
Abstract
Description
Claims
Application Information

- R&D
- Intellectual Property
- Life Sciences
- Materials
- Tech Scout
- Unparalleled Data Quality
- Higher Quality Content
- 60% Fewer Hallucinations
Browse by: Latest US Patents, China's latest patents, Technical Efficacy Thesaurus, Application Domain, Technology Topic, Popular Technical Reports.
© 2025 PatSnap. All rights reserved.Legal|Privacy policy|Modern Slavery Act Transparency Statement|Sitemap|About US| Contact US: help@patsnap.com