Refinery matched coal-to-hydrogen sulfur-tolerant shift methanation integrated process
A technology for sulfur-resistant methanation and sulfur-resistant shift, which is applied to the integrated process of coal-to-hydrogen sulfur-resistant shift methanation in refineries, can solve problems affecting the long-term stable operation of the device, the inability to adjust the hydrogen output flexibly, increasing the investment of the device and Land occupation and other issues, to achieve the effect of maintaining long-term stable operation, ensuring long-term stable operation and good economic benefits
- Summary
- Abstract
- Description
- Claims
- Application Information
AI Technical Summary
Problems solved by technology
Method used
Image
Examples
Embodiment Construction
[0025] The present invention will be further described in detail below in conjunction with the accompanying drawings and embodiments.
[0026] The equipment used in the coal-to-hydrogen sulfur-resistant shift methanation integrated process for the refinery in this embodiment includes: a coal gasification unit, a sulfur-resistant shift methanation unit, an acid gas removal unit, and a PSA unit. Coal gasification unit, sulfur-tolerant shift methanation unit, acid gas removal unit and PSA unit are connected sequentially from upstream to downstream. Among them, the devices and operating principles adopted by the coal gasification unit, the acid gas removal unit and the PSA unit are all existing mature technologies, and will not be described again.
[0027] The following is a detailed description of the equipment and operating principles used in the sulfur-tolerant shift methanation unit.
[0028] In this embodiment, the sulfur-resistant shift methanation unit includes a pre-steam g...
PUM
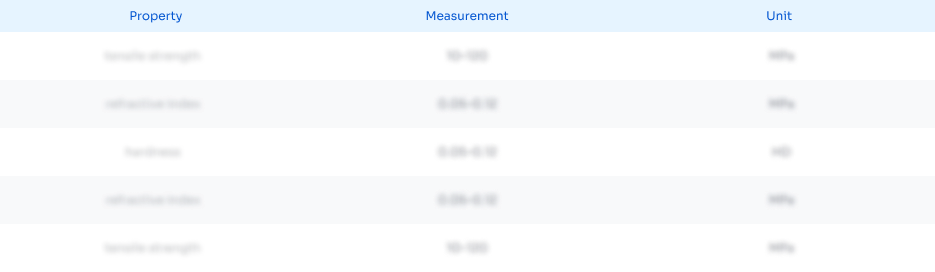
Abstract
Description
Claims
Application Information

- Generate Ideas
- Intellectual Property
- Life Sciences
- Materials
- Tech Scout
- Unparalleled Data Quality
- Higher Quality Content
- 60% Fewer Hallucinations
Browse by: Latest US Patents, China's latest patents, Technical Efficacy Thesaurus, Application Domain, Technology Topic, Popular Technical Reports.
© 2025 PatSnap. All rights reserved.Legal|Privacy policy|Modern Slavery Act Transparency Statement|Sitemap|About US| Contact US: help@patsnap.com