Spinning process for automobile aluminum alloy hub
A technology of aluminum alloy wheel hub and spinning process, which is applied in the direction of rim, vehicle parts, transportation and packaging, etc. It can solve the problems of large influence on the machining accuracy of aluminum alloy wheel hub blanks, large energy consumption, and insufficient spinning, etc., to reduce The investment of equipment and labor can improve the effective utilization rate, and the effect of not easy spinning is not in place
- Summary
- Abstract
- Description
- Claims
- Application Information
AI Technical Summary
Problems solved by technology
Method used
Image
Examples
Embodiment Construction
[0030] Such as Figure 3 to Figure 9 As shown, the automobile aluminum alloy wheel hub spinning process of the present invention comprises the following steps: (1) heating the spinning mold 1 to make its temperature reach 270-290°C, spraying a release agent on the surface of the spinning mold 1, and simultaneously turning the mold from the casting Take out the aluminum alloy wheel blank 10 from the mold and put it directly into the heating furnace to continue heating. The temperature of the aluminum alloy wheel blank 10 taken out from the casting mold is about 260-290°C, and the hot (about 260-290°C) aluminum alloy wheel blank 10 Put it directly into the heating furnace and continue heating until the temperature of the aluminum alloy wheel blank reaches 355-375°C; (2) Use a manipulator to grab the aluminum alloy wheel blank 10 coming out of the heating furnace and place the aluminum alloy wheel blank 10 on the spinning mold 1, control the upper tail top tooling above the spinn...
PUM
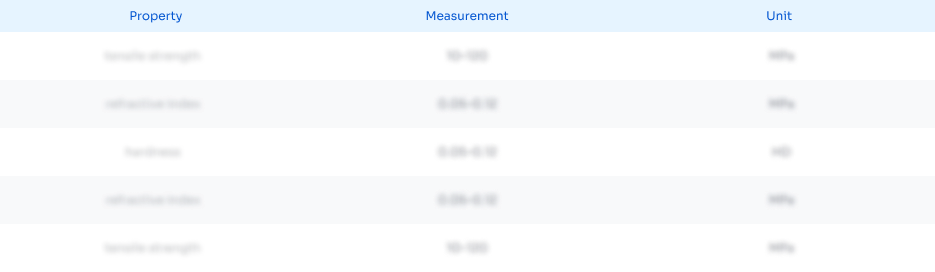
Abstract
Description
Claims
Application Information

- R&D
- Intellectual Property
- Life Sciences
- Materials
- Tech Scout
- Unparalleled Data Quality
- Higher Quality Content
- 60% Fewer Hallucinations
Browse by: Latest US Patents, China's latest patents, Technical Efficacy Thesaurus, Application Domain, Technology Topic, Popular Technical Reports.
© 2025 PatSnap. All rights reserved.Legal|Privacy policy|Modern Slavery Act Transparency Statement|Sitemap|About US| Contact US: help@patsnap.com