Abrasion-resistant clamping plate and preparation method thereof
A splint and nickel plate technology, applied in the field of wear-resistant materials, can solve the problems of difficult casting quality control, unsatisfactory use effect, plastic deformation of the splint, etc., and achieve the effect of reducing the frequency of replacing the splint, increasing the strength, and increasing the toughness and strength.
- Summary
- Abstract
- Description
- Claims
- Application Information
AI Technical Summary
Problems solved by technology
Method used
Examples
Embodiment 1
[0026] A preparation method of a wear-resistant splint, comprising the following steps:
[0027] S1, add clean and dry ordinary steel scrap, pig iron, stainless steel scrap, magnesium ingot, ferromanganese, ferromolybdenum, nickel plate, titanium ingot, and waste electrode for carbon increase into the furnace, heat and melt, and adjust the composition to the percentage of each component For: carbon 2.9%, silicon 0.55%, magnesium 0.6%, manganese 0.55%, chromium 16%, molybdenum 0.5%, nickel 0.16%, titanium 0.16%, phosphorus 0.02%, sulfur 0.02%, the balance is iron, the temperature rises To 1550°C, add preheated ferrosilicon for precipitation deoxidation, 2 minutes before tapping the iron, use the method of deep insertion of aluminum wire for diffusion deoxidation, and then tap the iron;
[0028] S2, put the high-efficiency composite modifier and rare earth at the bottom of the ladle to modify the molten steel, and then pour the molten steel into the ingot mold. The pouring tempe...
Embodiment 2
[0031] A preparation method of a wear-resistant splint, comprising the following steps:
[0032] S1, add clean and dry ordinary steel scrap, pig iron, stainless steel scrap, magnesium ingot, ferromanganese, ferromolybdenum, nickel plate, titanium ingot, and waste electrode for carbon increase into the furnace, heat and melt, and adjust the composition to the percentage of each component For: carbon 2.0%, silicon 0.8%, magnesium 0.7%, manganese 0.8%, chromium 15%, molybdenum 0.7%, nickel 0.14%, titanium 0.1%, phosphorus 0.06%, sulfur 0.06%, the balance is iron, the temperature rises To 1600°C, add preheated ferrosilicon for precipitation deoxidation, 2 minutes before tapping the iron, use the method of deep insertion of aluminum wire for diffusion deoxidation, and then tap the iron;
[0033] S2, put the high-efficiency compound modifier and rare earth at the bottom of the ladle to modify the molten steel, and then pour the molten steel into the ingot mold. The pouring temperatu...
Embodiment 3
[0037] A preparation method of a wear-resistant splint, comprising the following steps:
[0038] S1, add clean and dry ordinary steel scrap, pig iron, stainless steel scrap, magnesium ingot, ferromanganese, ferromolybdenum, nickel plate, titanium ingot, and waste electrode for carbon increase into the furnace, heat and melt, and adjust the composition to the percentage of each component For: carbon 2.9%, silicon 0.4%, magnesium 0.4%, manganese 1.0%, chromium 14%, molybdenum 1.0%, nickel 0.1%, titanium 0.20%, phosphorus 0.04%, sulfur 0.04%, the balance is iron, the temperature rises To 1500°C, add preheated ferrosilicon for precipitation deoxidation, 2 minutes before tapping the iron, use the method of deep insertion of aluminum wire for diffusion deoxidation, and then tap the iron;
[0039] S2, put the high-efficiency composite modifier and rare earth at the bottom of the ladle to modify the molten steel, and then pour the molten steel into the ingot mold. The pouring temperat...
PUM
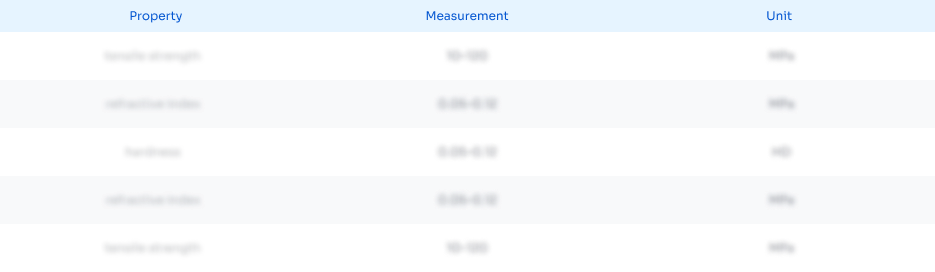
Abstract
Description
Claims
Application Information

- R&D
- Intellectual Property
- Life Sciences
- Materials
- Tech Scout
- Unparalleled Data Quality
- Higher Quality Content
- 60% Fewer Hallucinations
Browse by: Latest US Patents, China's latest patents, Technical Efficacy Thesaurus, Application Domain, Technology Topic, Popular Technical Reports.
© 2025 PatSnap. All rights reserved.Legal|Privacy policy|Modern Slavery Act Transparency Statement|Sitemap|About US| Contact US: help@patsnap.com