Control method for embedded permanent magnet synchronous motor
A technology of permanent magnet synchronous motor and control method, applied in the direction of motor control, motor generator control, AC motor control, etc., can solve problems such as the lack of real-time and accurate use of motor parameters, the influence of motor torque accuracy and motor operation efficiency, etc.
- Summary
- Abstract
- Description
- Claims
- Application Information
AI Technical Summary
Problems solved by technology
Method used
Image
Examples
Embodiment Construction
[0082] The control method of embedded permanent magnet synchronous motor, its control block diagram (such as figure 1 As shown) includes a resolver module 1, a temperature sensor module 2, a stator resistance calculation module 3, a Clark transformation module 4, a Park transformation module 5, a stator inductance calculation look-up module 6, a permanent magnet flux linkage calculation module 7, and a torque calculation module 8. Current I* calculation module 9, current angle calculation module 10, robust decoupling controller module 11, PWM modulation module 12, three-phase inverter bridge module 13;
[0083] 1) Resolver module
[0084]The resolver is installed on the embedded permanent magnet synchronous motor, the rotor position θ of the permanent magnet synchronous motor can be measured through the resolver, and the rotor position θ can be differentiated to obtain the speed w of the permanent magnet synchronous motor e ;
[0085] 2) Temperature sensor module
[0086] A...
PUM
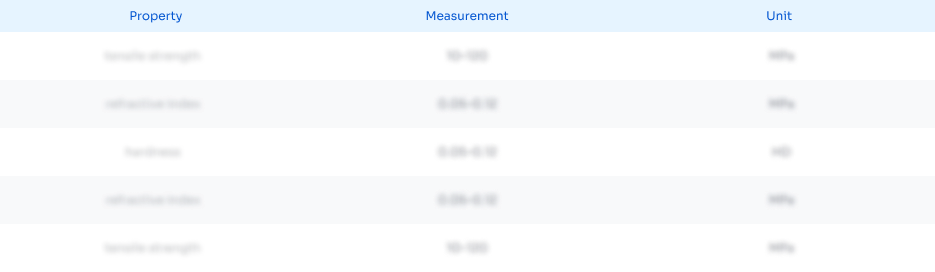
Abstract
Description
Claims
Application Information

- R&D
- Intellectual Property
- Life Sciences
- Materials
- Tech Scout
- Unparalleled Data Quality
- Higher Quality Content
- 60% Fewer Hallucinations
Browse by: Latest US Patents, China's latest patents, Technical Efficacy Thesaurus, Application Domain, Technology Topic, Popular Technical Reports.
© 2025 PatSnap. All rights reserved.Legal|Privacy policy|Modern Slavery Act Transparency Statement|Sitemap|About US| Contact US: help@patsnap.com