Electrolytic zinc blackening control method
A control method, electro-galvanizing technology, applied in electrolytic process, electrolytic components, cells, etc., can solve problems such as blackening of galvanized steel, and achieve the effect of improving the quality of protection
- Summary
- Abstract
- Description
- Claims
- Application Information
AI Technical Summary
Problems solved by technology
Method used
Image
Examples
Embodiment
[0032] A method for controlling blackening of electro-galvanized coatings, comprising the steps of:
[0033] Step 1, degreasing: put the workpiece into gasoline or industrial alcohol with a mass concentration of 90% and soak it at room temperature for 5-10 minutes to remove surface oil stains; then perform electrolytic degreasing;
[0034] Step 2, hot water washing: Use hot water at 90°C-100°C to clean the surface of the workpiece for 30-60s to remove residual lye and salt on the surface of the workpiece;
[0035] Step 3, rust removal: use rust removal solution to remove rust on the surface of the workpiece;
[0036] Step 4, cold water washing: use 15-20°C running cold water for countercurrent rinsing for 30-60s;
[0037] Step 5, deionized water washing: before entering the galvanizing tank, the workpiece is cleaned with deionized water at 15°C-30°C for 30-60s to ensure that no other ions on the surface of the workpiece enter the plating tank;
[0038] Step 6, galvanizing: u...
PUM
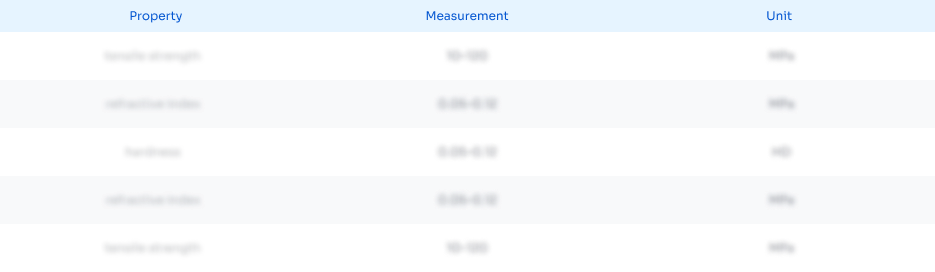
Abstract
Description
Claims
Application Information

- R&D
- Intellectual Property
- Life Sciences
- Materials
- Tech Scout
- Unparalleled Data Quality
- Higher Quality Content
- 60% Fewer Hallucinations
Browse by: Latest US Patents, China's latest patents, Technical Efficacy Thesaurus, Application Domain, Technology Topic, Popular Technical Reports.
© 2025 PatSnap. All rights reserved.Legal|Privacy policy|Modern Slavery Act Transparency Statement|Sitemap|About US| Contact US: help@patsnap.com