PU plastic-coated steel wire, and preparation method and application thereof
A steel wire and plastic coating technology, applied in the field of materials, can solve the problems of weak bonding between the outer coating and the inner steel wire, affecting the appearance and quality, and poor viscosity of the outer coating, so as to ensure the strength, improve the viscosity, and improve the bonding. performance effect
- Summary
- Abstract
- Description
- Claims
- Application Information
AI Technical Summary
Problems solved by technology
Method used
Examples
Embodiment 1
[0025] In the embodiment of the present invention, a PU plastic-coated steel wire includes a steel wire and an outer covering layer located on the periphery of the steel wire; the masterbatch of the outer covering layer is made of the following raw materials in parts by weight: 34 parts of polyurethane resin, organic solvent 8 parts, 8 parts of rosin glyceride, 1.5 parts of dibutyltin dilaurate, 12 parts of fiber silk.
[0026] Wherein, the organic solvent is acetone, and the fiber filaments are chemical fibers.
[0027] Wherein, the preparation method of the masterbatch of the outer cladding layer is as follows:
[0028] 1) Melt the polyurethane resin and keep it molten;
[0029] 2) Add rosin glyceride to the molten polyurethane resin, mix and stir for 8 minutes, the stirring speed is 400rpm, then add dibutyltin dilauric acid, mix and stir for 12min, the stirring speed is 600rpm, finally add the organic solvent, mix and stir for 3min, stir Speed is 110rpm, obtains polyure...
Embodiment 2
[0037] In the embodiment of the present invention, a PU plastic-coated steel wire includes a steel wire and an outer covering layer located on the periphery of the steel wire; the masterbatch of the outer covering layer is made of the following raw materials in parts by weight: 38 parts of polyurethane resin, organic solvent 10 parts, rosin glyceride 10 parts, dibutyltin dilaurate 1.7 parts, fiber silk 16 parts.
[0038] Wherein, the organic solvent is acetone, and the fiber filaments are natural fibers.
[0039] Wherein, the preparation method of the masterbatch of the outer cladding layer is as follows:
[0040] 1) Melt the polyurethane resin and keep it molten;
[0041] 2) Add rosin glyceride to the molten polyurethane resin, mix and stir for 10 minutes, the stirring speed is 500rpm, then add dibutyltin dilauric acid, mix and stir for 13min, the stirring speed is 650rpm, finally add the organic solvent, mix and stir for 4min, stir Speed is 150rpm, obtains polyurethane m...
Embodiment 3
[0049] In the embodiment of the present invention, a PU plastic-coated steel wire includes a steel wire and an outer covering layer located on the periphery of the steel wire; the masterbatch of the outer covering layer is made of the following raw materials in parts by weight: 41 parts of polyurethane resin, organic solvent 14 parts, rosin glyceride 12 parts, dibutyltin dilaurate 1.8 parts, fiber silk 18 parts.
[0050] Wherein, the organic solvent is acetone, and the fiber filaments are natural fibers.
[0051] Wherein, the preparation method of the masterbatch of the outer cladding layer is as follows:
[0052] 1) Melt the polyurethane resin and keep it molten;
[0053] 2) Add rosin glyceride to the molten polyurethane resin, mix and stir for 9 minutes, the stirring speed is 500rpm, then add dibutyltin dilauric acid, mix and stir for 15min, the stirring speed is 700rpm, finally add the organic solvent, mix and stir for 5min, stir Speed is 160rpm, obtains polyurethane mi...
PUM
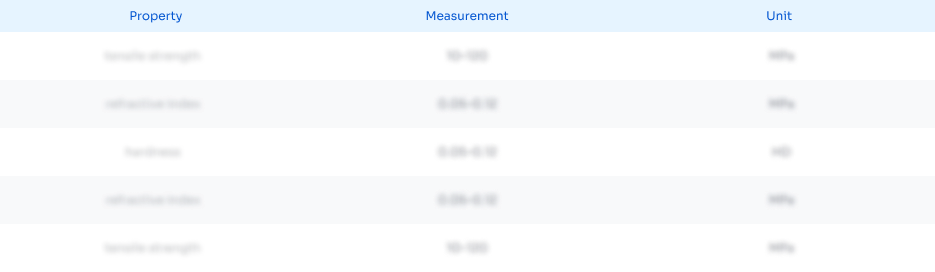
Abstract
Description
Claims
Application Information

- R&D
- Intellectual Property
- Life Sciences
- Materials
- Tech Scout
- Unparalleled Data Quality
- Higher Quality Content
- 60% Fewer Hallucinations
Browse by: Latest US Patents, China's latest patents, Technical Efficacy Thesaurus, Application Domain, Technology Topic, Popular Technical Reports.
© 2025 PatSnap. All rights reserved.Legal|Privacy policy|Modern Slavery Act Transparency Statement|Sitemap|About US| Contact US: help@patsnap.com