Method for removing iron in noble metal rhodium recovery process
A precious metal, ferric chloride technology, applied in the direction of improving process efficiency, can solve the problems of complex analysis process, reducing the recovery rate of precious metal rhodium, difficult recovery and purification of precious metal rhodium, etc., and achieves high purity, high recovery rate and simple process. Effect
- Summary
- Abstract
- Description
- Claims
- Application Information
AI Technical Summary
Problems solved by technology
Method used
Examples
Embodiment 1
[0028] concentrating and incinerating the recovered triphenylphosphine acetylacetonate rhodium carbonyl catalyst waste solution to obtain a mixture; chlorinating the mixture to obtain a mixture of rhodium chloride and ferric chloride. The rhodium chloride mixture containing a certain amount of ferric chloride after taking 20.9g of chlorination (simultaneously as sample No. 0 sample) is dissolved in 100ml mass concentration 1% hydrochloric acid solution, adds 36.3g sodium chloride, at 50 ℃ of conditions Stir to dissolve completely. After removing the insoluble matter by suction filtration, the filtrate was decompressed to remove most of the liquid, and then dried in an oven at 110°C to obtain a rose-red solid. The obtained solid was ground into powder and then transferred to 200ml of absolute ethanol, stirred and dissolved at 50°C for 1 hour, and then suction-filtered. The recovered sodium chlororhodium acid sample 1 was obtained, and the sample 1 was ground into powder again,...
Embodiment 2
[0033] Weigh 20.9g of the rhodium chloride mixture containing a certain amount of ferric chloride prepared in Example 1 and dissolve it in 100ml of 1% hydrochloric acid solution, add 36.3g of sodium chloride, stir and fully dissolve at 50°C. After removing the insoluble matter by suction filtration, the filtrate was decompressed to remove most of the liquid, and then dried in an oven at 110°C to obtain a rose-red solid. The obtained solid was ground into powder and then transferred to 200ml of absolute ethanol, stirred and dissolved at 50°C for 1 hour, and then suction-filtered. To obtain the recovered sodium chlororhodium acid sample, transfer the dried sodium chlororhodium acid to a reduction furnace, replace it with nitrogen, and heat up to 600°C and pass in hydrogen for 30 minutes to obtain elemental rhodium. The recovery rate of rhodium is 99.0-99.5%, and the purity is 99.92%. %.
Embodiment 3
[0035] Weigh 20.9g of the rhodium chloride mixture containing a certain amount of ferric chloride prepared in Example 1 and dissolve it in 100ml of 1.2% hydrochloric acid solution, add 37.3g of sodium chloride, stir and fully dissolve at 50°C. After removing the insoluble matter by suction filtration, the filtrate was decompressed to remove most of the liquid, and then dried in an oven at 110°C to obtain a rose-red solid. The obtained solid was ground into powder and transferred to 200ml of absolute ethanol, stirred and dissolved at 40°C for 1.5h, and then suction filtered; this washing step was repeated twice. To obtain the recovered rhodium chlororhodium sample, transfer the dried rhodium chlororhodium to the reduction furnace, replace it with nitrogen, heat up to 620°C, and pass in hydrogen for 30 minutes to obtain elemental rhodium. The recovery rate of rhodium is 98.7-99.3%, and the purity is 99.93%. %.
PUM
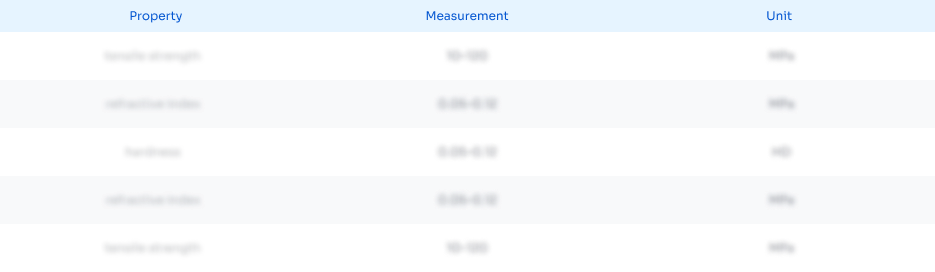
Abstract
Description
Claims
Application Information

- R&D
- Intellectual Property
- Life Sciences
- Materials
- Tech Scout
- Unparalleled Data Quality
- Higher Quality Content
- 60% Fewer Hallucinations
Browse by: Latest US Patents, China's latest patents, Technical Efficacy Thesaurus, Application Domain, Technology Topic, Popular Technical Reports.
© 2025 PatSnap. All rights reserved.Legal|Privacy policy|Modern Slavery Act Transparency Statement|Sitemap|About US| Contact US: help@patsnap.com