Electric spark and electrolytic continuous machining method and tool for efficient plane milling
A processing method and electric spark technology, applied in the field of EDM, can solve the problems of time consumption, reduce processing efficiency, and cannot be reused, and achieve the effects of easy disassembly and replacement, reduced loss, and improved processing efficiency.
- Summary
- Abstract
- Description
- Claims
- Application Information
AI Technical Summary
Problems solved by technology
Method used
Image
Examples
Embodiment Construction
[0031] figure 1 In the schematic diagram of continuous EDM electrolysis shown in the diagram, the pipeline of the electrolyte tank is connected to the tool through the electrolyte inlet pipe 1 and the connecting cover 3, and the connecting cover 3, electrolytic electrode 4 and copper-tungsten alloy EDM electrode 6 use hexagon socket screws 2 connections. One side of the copper-tungsten alloy EDM electrode 6 is the rake face, which ensures that the copper-tungsten alloy EDM electrode 6 first performs EDM machining on the surface of the workpiece to be processed during horizontal feeding.
[0032] figure 2 Shown is a schematic diagram of the comparison between electrolytic machining and continuous EDM. from figure 2 It can be seen from (a) that when the processing tool moves horizontally, there is a large initial processing gap between the ordinary electrolysis electrode 7 and the workpiece surface to be processed h 1 , to ensure that processed products can be quickly dis...
PUM
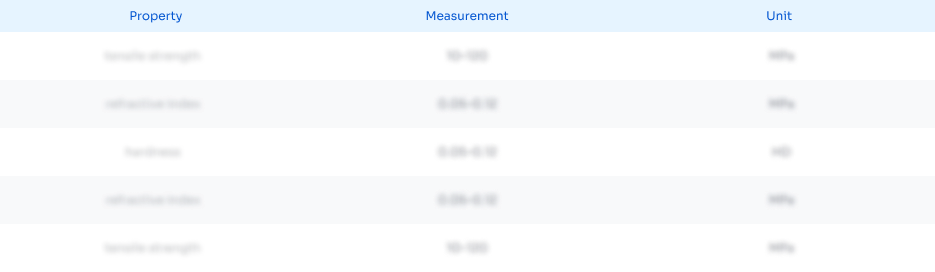
Abstract
Description
Claims
Application Information

- Generate Ideas
- Intellectual Property
- Life Sciences
- Materials
- Tech Scout
- Unparalleled Data Quality
- Higher Quality Content
- 60% Fewer Hallucinations
Browse by: Latest US Patents, China's latest patents, Technical Efficacy Thesaurus, Application Domain, Technology Topic, Popular Technical Reports.
© 2025 PatSnap. All rights reserved.Legal|Privacy policy|Modern Slavery Act Transparency Statement|Sitemap|About US| Contact US: help@patsnap.com