Chlorine-containing rubber composition as well as application and preparation method thereof
A rubber composition and a technology for the composition, applied in the rubber field, can solve the problems of reduced physical and mechanical properties, difficult processing, limited range of chlorine content, etc., and achieve fast vulcanization speed, less addition, and improved physical or chemical properties. Effect
- Summary
- Abstract
- Description
- Claims
- Application Information
AI Technical Summary
Problems solved by technology
Method used
Image
Examples
Embodiment 22
[0123] The mixing process of Example 22 is as follows: the initial temperature of the internal mixer is set to 85° C., the rotating speed is 40 rpm, and all dry additives and liquid additives except TDD and NC are successively added, mixed for 3 minutes, and then Add the rubber matrix, after the mixing power is stable, add TDD and NC, mix for 1 minute, then remove the glue, and then on the open mill, thin pass, unload, cool, stop for 24 hours, and then return to knead to release the tablet.
Embodiment 23
[0124] The mixing process of Example 23 is as follows: set the internal mixer to an initial temperature of 85°C and a rotational speed of 40 rpm, add all dry additives and liquid additives except sulfur and DE-TU successively, and mix for 3 minutes , then add the rubber matrix, discharge the rubber after the mixing power is stable, add sulfur and DE-TU to the open mill with a roller temperature of 70°C, make triangular bags three times, and then remove the film after thinning, cool, and park for 24 hours before returning Make a piece.
[0125] All tests were prepared and tested according to the standard. The vulcanization method is molding vulcanization, the vulcanization temperature is 165°C, the pressure is 16MPa, the time is Tc90+1min, and the test is carried out after 16 hours of parking. The vulcanization time of the compression set sample is Tc90+5min. The performance data of each test sample is shown in Table 8:
[0126] Table 8
[0127]
[0128] Data Analysis: By...
Embodiment 26~28
[0131] The rubber composition formula component of embodiment 26~28 is as shown in table 9: (wherein listed relative to every 100 parts by weight of rubber matrix, the parts by weight of each component used)
[0132] Table 9
[0133]
[0134] The mixing process of embodiment 26~28 is as follows:
[0135] Set the initial temperature of the internal mixer to 85°C and the speed to 40 rpm, add all the dry additives and liquid additives except BIBP and TAIC successively, mix for 3 minutes, then add the rubber matrix, and wait until the mixing power is stable Finally, add BIBP and TAIC, knead for 1 minute and remove the glue, then on the open mill, thin pass, unload, cool, stop for 24 hours, and then return to knead to release the tablet.
[0136] All tests were prepared and tested according to the standard. The vulcanization method is molding vulcanization, the vulcanization temperature is 165°C, the pressure is 16MPa, the time is Tc90+1min, and the test is carried out after 1...
PUM
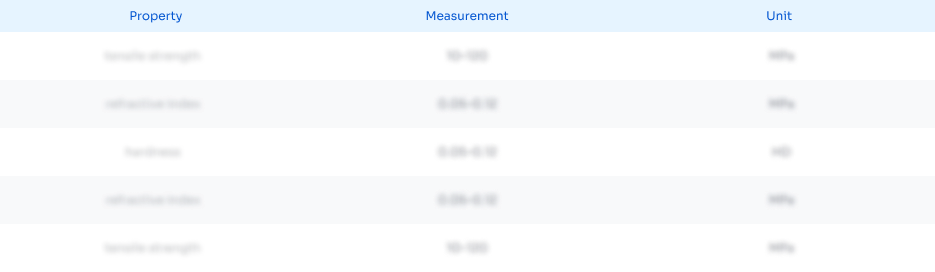
Abstract
Description
Claims
Application Information

- R&D Engineer
- R&D Manager
- IP Professional
- Industry Leading Data Capabilities
- Powerful AI technology
- Patent DNA Extraction
Browse by: Latest US Patents, China's latest patents, Technical Efficacy Thesaurus, Application Domain, Technology Topic, Popular Technical Reports.
© 2024 PatSnap. All rights reserved.Legal|Privacy policy|Modern Slavery Act Transparency Statement|Sitemap|About US| Contact US: help@patsnap.com