Optical Remote Sensor Using Structural Deformation to Compensate Optical System Misalignment
An optical remote sensor and optical system technology, applied in the field of space remote sensing, can solve the problems of optical components deviating from the optimal position, surface shape accuracy error, difficulty in ensuring large-diameter optical components, etc., so as to achieve the effect of unaffected imaging quality.
- Summary
- Abstract
- Description
- Claims
- Application Information
AI Technical Summary
Problems solved by technology
Method used
Image
Examples
Embodiment Construction
[0012] The technical solutions in the embodiments of the present invention will be clearly and completely described below in conjunction with the accompanying drawings in the embodiments of the present invention. Obviously, the described embodiments are only part of the embodiments of the present invention, not all of them. Based on the implementation manners in the present invention, all other implementation manners obtained by persons of ordinary skill in the art without making creative efforts belong to the scope of protection of the present invention.
[0013] Please refer to figure 1 , the schematic diagram of the optical path of the optical remote sensor that uses structural deformation to compensate for the misalignment of the optical system provided by the preferred embodiment of the present invention. The optical remote sensor adopts a coaxial reflective optical system. For example, such as figure 1 As shown, the optical remote sensor that uses structural deformation...
PUM
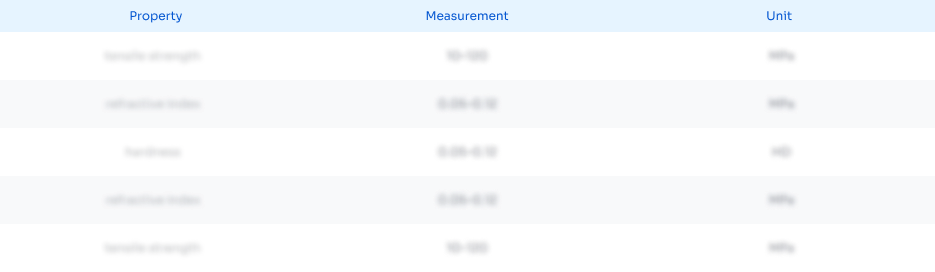
Abstract
Description
Claims
Application Information

- R&D
- Intellectual Property
- Life Sciences
- Materials
- Tech Scout
- Unparalleled Data Quality
- Higher Quality Content
- 60% Fewer Hallucinations
Browse by: Latest US Patents, China's latest patents, Technical Efficacy Thesaurus, Application Domain, Technology Topic, Popular Technical Reports.
© 2025 PatSnap. All rights reserved.Legal|Privacy policy|Modern Slavery Act Transparency Statement|Sitemap|About US| Contact US: help@patsnap.com