Preparation method and application method of after-finishing solution for fabrics
A technology for finishing and fabrics, applied in the field of fabric finishing liquid preparation, can solve the problems of free formaldehyde and the decrease of fabric strength, and achieve the effect of improved wrinkle recovery performance and low strength loss
- Summary
- Abstract
- Description
- Claims
- Application Information
AI Technical Summary
Problems solved by technology
Method used
Examples
Embodiment 1
[0019] The preparation method of the fabric finishing solution comprises step a, adding 18 g of polypropylene glycol and 3 drops of catalyst dibutyltin dilaurate into a four-necked flask equipped with a magnet, a thermometer, a reflux condenser and a constant pressure dropping funnel, and heating to 80°C, after mixing well, slowly add 8g of isophorone diisocyanate dropwise under the protection of nitrogen, after 1.5h of reaction, add 1.98g of hydrophilic chain extender N-methyldiethanolamine dropwise, and react for 3h to generate polyurethane prepolymer The prepared polyurethane prepolymer was cooled to 40°C, then added 1.08g of neutralizing agent acetic acid, and reacted for 30min; added 3.9g of silane coupling agent γ-aminopropyltriethoxysilane, and heated to 45°C, React for 40 minutes; finally add 90 ml of deionized water and emulsify at high speed for 30 minutes to obtain cationic silicone-modified waterborne polyurethane.
[0020] b. Compounding cationic organosilicon-mod...
Embodiment 2
[0024] The preparation method of the fabric finishing solution comprises step a, adding 20 g of polypropylene glycol and 3 drops of catalyst dibutyltin dilaurate into a four-necked flask equipped with a magnet, a thermometer, a reflux condenser and a constant pressure dropping funnel, and heating to 80°C, after mixing well, slowly add 8g of isophorone diisocyanate dropwise under the protection of nitrogen, after 1.5h of reaction, add 1.68g of hydrophilic chain extender N-methyldiethanolamine dropwise, and react for 3h to generate polyurethane prepolymer Cool the prepared polyurethane prepolymer to 40°C, then add 0.88g of neutralizing agent acetic acid, react for 30min, add 4.9g of silane coupling agent γ-aminopropyltriethoxysilane, heat up to 45°C, React for 40 minutes; finally add 90 ml of deionized water and emulsify at high speed for 30 minutes to obtain cationic silicone-modified waterborne polyurethane.
[0025] b. Compound cationic organosilicon-modified water-based poly...
Embodiment 3
[0029] The preparation method of the fabric finishing solution comprises step a, adding 15 g of polypropylene glycol and 3 drops of catalyst dibutyltin dilaurate into a four-necked flask equipped with a magnet, a thermometer, a reflux condenser and a constant pressure dropping funnel, and heating to 80°C, after mixing well, slowly add 9g of isophorone diisocyanate dropwise under the protection of nitrogen, after 1.5h of reaction, add 2.28g of hydrophilic chain extender N-methyldiethanolamine dropwise, and react for 3h to generate polyurethane prepolymer Cool the prepared polyurethane prepolymer to 40°C, then add 1.58g of neutralizing agent acetic acid, react for 30min, add 4.2g of silane coupling agent γ-aminopropyltriethoxysilane, heat up to 45°C, React for 40 minutes; finally add 90 ml of deionized water and emulsify at high speed for 30 minutes to obtain cationic silicone-modified waterborne polyurethane.
[0030] b. Compound cationic organosilicon-modified water-based poly...
PUM
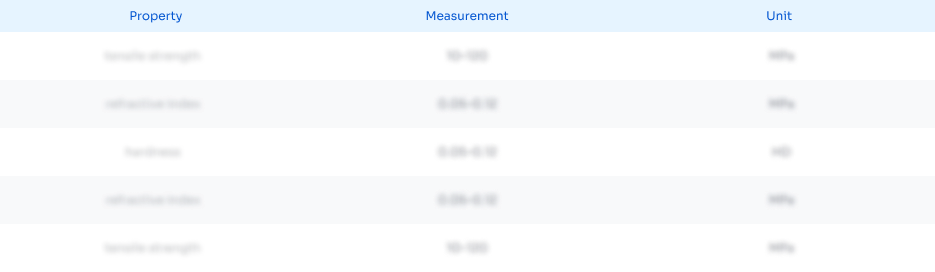
Abstract
Description
Claims
Application Information

- R&D
- Intellectual Property
- Life Sciences
- Materials
- Tech Scout
- Unparalleled Data Quality
- Higher Quality Content
- 60% Fewer Hallucinations
Browse by: Latest US Patents, China's latest patents, Technical Efficacy Thesaurus, Application Domain, Technology Topic, Popular Technical Reports.
© 2025 PatSnap. All rights reserved.Legal|Privacy policy|Modern Slavery Act Transparency Statement|Sitemap|About US| Contact US: help@patsnap.com