Assembly method for fillet welded joint at vertical positions of thin plates
A fillet weld and assembly method technology, applied in welding equipment, welding equipment, auxiliary devices, etc., can solve the problems of affecting the welding seam forming, slow welding speed, and large welding line energy, so as to improve the welding seam forming, reduce Deformation of the sheet, the effect of facilitating assembly
- Summary
- Abstract
- Description
- Claims
- Application Information
AI Technical Summary
Problems solved by technology
Method used
Examples
Embodiment Construction
[0019] In order to make the technical problems solved by the present invention, the technical solutions adopted and the technical effects achieved clearer, the technical solutions of the embodiments of the present invention will be further described in detail below. Obviously, the described embodiments are only a part of the embodiments of the present invention , but not all examples. Based on the embodiments of the present invention, all other embodiments obtained by those skilled in the art without making creative efforts belong to the protection scope of the present invention.
[0020] This embodiment provides a method for assembling a fillet weld in a vertical position of a thin plate, which includes the following steps:
[0021] S1. Closely attach the long side of the first thin plate to the surface of the second thin plate, place the two thin plates in a T-shaped joint, and use the support structure to fix the two thin plates respectively;
[0022] S2, cleaning the weld...
PUM
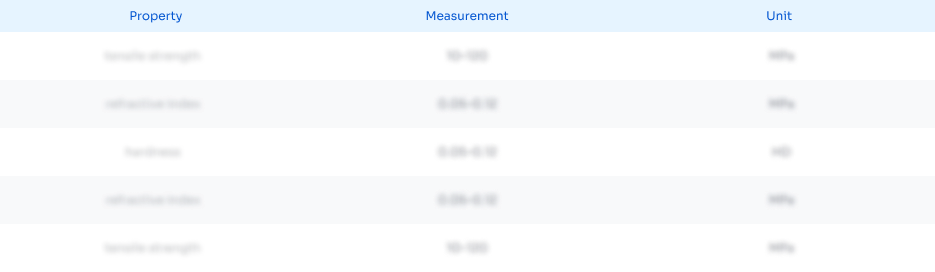
Abstract
Description
Claims
Application Information

- R&D
- Intellectual Property
- Life Sciences
- Materials
- Tech Scout
- Unparalleled Data Quality
- Higher Quality Content
- 60% Fewer Hallucinations
Browse by: Latest US Patents, China's latest patents, Technical Efficacy Thesaurus, Application Domain, Technology Topic, Popular Technical Reports.
© 2025 PatSnap. All rights reserved.Legal|Privacy policy|Modern Slavery Act Transparency Statement|Sitemap|About US| Contact US: help@patsnap.com