Online soot blowing device for waste heat boiler for sintering vertical cold furnace
A technology of waste heat boiler and soot blowing device, which is applied in the direction of combustion method, removal of solid residue, treatment of combustion products, etc. It can solve the problems of affecting boiler evaporation heat transfer efficiency, unknown blowing effect, insufficient pressure, etc., and achieves accurate Purging technology and implementation status monitoring, eliminating the possibility of water, increasing the effect of purging area
- Summary
- Abstract
- Description
- Claims
- Application Information
AI Technical Summary
Problems solved by technology
Method used
Image
Examples
Embodiment 1
[0018] Example 1: see figure 1 , figure 2 , An online soot blowing device for a sintered vertical cooling waste heat boiler, the soot blowing device includes a waste heat boiler 1, a steam drum 2, a vertical cooling furnace 22, an induced draft fan 23, and a purge assembly. The waste heat boiler 1 adopts a vertical arrangement, and the steam The package 2 is installed on the top of the waste heat boiler 1 and arranged on the boiler support near the vertical cooling furnace 22. The purge assembly includes three purge devices, namely the high temperature purge device 3, the low temperature purge device 4 and the economizer purge device. Sweeping device 5, the waste heat boiler 1 is provided with a high temperature evaporator, a low temperature evaporator and an economizer evaporator, the high temperature evaporator is connected with a high temperature purge device, and the low temperature evaporator is connected with a low temperature purge device 4. The coaler 19 is connected to...
PUM
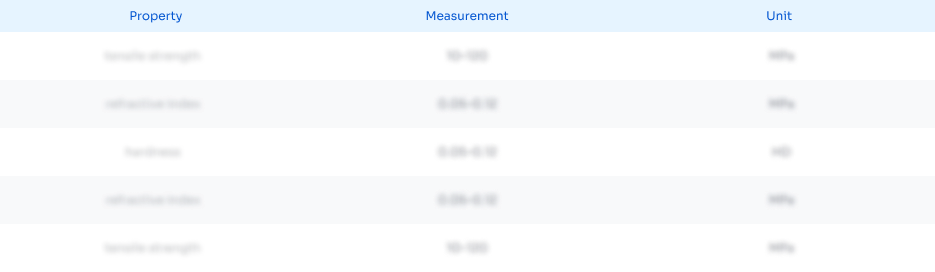
Abstract
Description
Claims
Application Information

- R&D
- Intellectual Property
- Life Sciences
- Materials
- Tech Scout
- Unparalleled Data Quality
- Higher Quality Content
- 60% Fewer Hallucinations
Browse by: Latest US Patents, China's latest patents, Technical Efficacy Thesaurus, Application Domain, Technology Topic, Popular Technical Reports.
© 2025 PatSnap. All rights reserved.Legal|Privacy policy|Modern Slavery Act Transparency Statement|Sitemap|About US| Contact US: help@patsnap.com