Production method for abrasion-resistant anti-fouling knitting needle
A wear-resistant and anti-fouling technology, which is applied in the field of knitting needle manufacturing, can solve the problems of poor wear resistance and achieve the effects of improving strength and toughness, preventing cracking tendency, and improving malleability
- Summary
- Abstract
- Description
- Claims
- Application Information
AI Technical Summary
Problems solved by technology
Method used
Examples
Embodiment Construction
[0016] The technical solutions in the embodiments of the present invention will be clearly and completely described below, obviously, the described embodiments are only some of the embodiments of the present invention, not all of the embodiments.
[0017] A method for preparing wear-resistant and anti-fouling knitting needles, comprising the following steps;
[0018] Step 1: Melting and casting steel ingots; use a certain proportion of metal elements to melt and cast steel ingots, and use the steel ingots cast after melting in an induction furnace as consumable electrodes and place them in the electroslag remelting device for electroslag remelting, and the liquid metal passes through the slag The slag layer of the pool falls into the water-cooled crystallizer below, and then re-solidifies into steel ingots; the specific material ratio of steel ingots is as follows: the mass percentage of C element is 0.8-1.2%, the mass percentage of Si element is 0.1-0.5%, The mass percentage ...
PUM
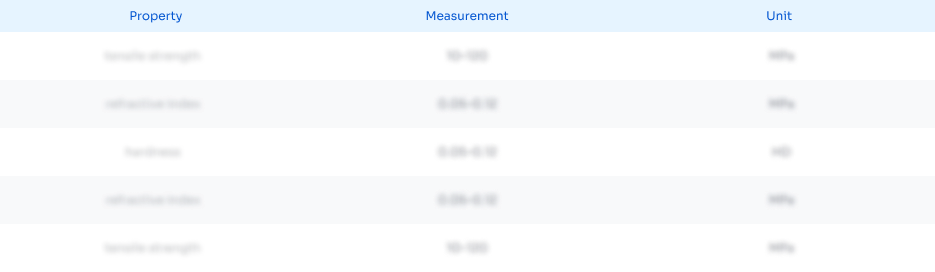
Abstract
Description
Claims
Application Information

- R&D
- Intellectual Property
- Life Sciences
- Materials
- Tech Scout
- Unparalleled Data Quality
- Higher Quality Content
- 60% Fewer Hallucinations
Browse by: Latest US Patents, China's latest patents, Technical Efficacy Thesaurus, Application Domain, Technology Topic, Popular Technical Reports.
© 2025 PatSnap. All rights reserved.Legal|Privacy policy|Modern Slavery Act Transparency Statement|Sitemap|About US| Contact US: help@patsnap.com