Basalt fiber reinforced recycled concrete
A technology of recycled concrete and basalt fiber, applied in the field of engineering materials, can solve the problems of recycled concrete strength, impermeability and impact resistance, low freeze-thaw resistance, etc., achieve good compressive strength, protect the environment, and improve the effect of compressive strength
- Summary
- Abstract
- Description
- Claims
- Application Information
AI Technical Summary
Problems solved by technology
Method used
Image
Examples
Embodiment 1
[0023] Prepare raw materials, which are composed of the following components by weight: 500 parts of recycled coarse aggregate, 400 parts of river sand, 400 parts of ceramsite, 350 parts of ordinary portland cement, 40 parts of fly ash, 10 parts of silica fume, mineral powder 10 parts, 3 parts of water reducer, 8 parts of basalt fiber with a length of 10 mm and a diameter of 15 μm, and 180 parts of water.
[0024] Add recycled coarse aggregate + ceramsite + river sand + cement + fly ash + silica fume + mineral powder in the forced mixer (stirring for 2 minutes) → basalt fiber (stirring for 3 minutes) → water and water reducer (stirring 2 minutes) → the preparation is completed, and the mold is loaded. Put the mold on a vibrating table to vibrate, and the slurry on the surface shall prevail. After one day, remove the mold and put it in the curing room for curing for 28 days.
Embodiment 2
[0026] Prepare raw materials, which are composed of the following components by weight: 600 parts of recycled coarse aggregate, 500 parts of river sand, 300 parts of ceramsite, 320 parts of ordinary Portland cement, 45 parts of fly ash, 12 parts of silica fume, mineral powder 15 parts, 4 parts of water reducer, 15 parts of basalt fiber with a length of 15 mm and a diameter of 10 μm, and 170 parts of water.
[0027] Add recycled coarse aggregate + ceramsite + river sand + cement + fly ash + silica fume + mineral powder in the forced mixer (stirring for 2 minutes) → basalt fiber (stirring for 3 minutes) → water and water reducer (stirring 2 minutes) → the preparation is completed, and the mold is loaded. Put the mold on a vibrating table to vibrate, and the slurry on the surface shall prevail. After one day, remove the mold and put it in the curing room for curing for 28 days.
Embodiment 3
[0029] Prepare raw materials, which are composed of the following components by weight: 700 parts of recycled coarse aggregate, 600 parts of river sand, 250 parts of ceramsite, 300 parts of ordinary portland cement, 50 parts of fly ash, 14 parts of silica fume, mineral powder 18 parts, 4 parts of water reducing agent, 12 parts of basalt fiber with a length of 18 mm and a diameter of 17 μm, and 165 parts of water.
[0030] Add recycled coarse aggregate + ceramsite + river sand + cement + fly ash + silica fume + mineral powder in the forced mixer (stirring for 2 minutes) → basalt fiber (stirring for 3 minutes) → water and water reducer (stirring 2 minutes) → the preparation is completed, and the mold is loaded. Put the mold on a vibrating table to vibrate, and the slurry on the surface shall prevail. After one day, remove the mold and put it in the curing room for curing for 28 days.
PUM
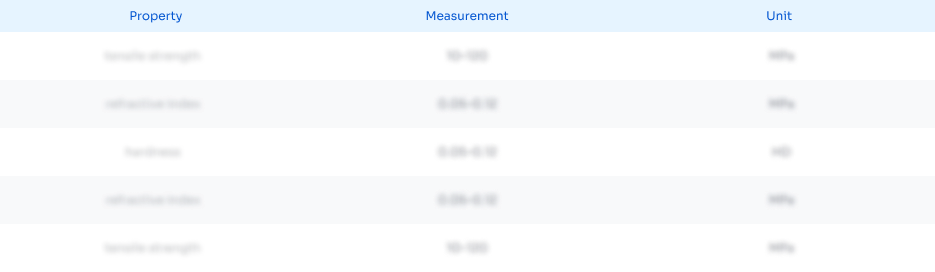
Abstract
Description
Claims
Application Information

- R&D
- Intellectual Property
- Life Sciences
- Materials
- Tech Scout
- Unparalleled Data Quality
- Higher Quality Content
- 60% Fewer Hallucinations
Browse by: Latest US Patents, China's latest patents, Technical Efficacy Thesaurus, Application Domain, Technology Topic, Popular Technical Reports.
© 2025 PatSnap. All rights reserved.Legal|Privacy policy|Modern Slavery Act Transparency Statement|Sitemap|About US| Contact US: help@patsnap.com