Polyurethane film with high wear resistance and preparation method of polyurethane film
A polyurethane film, high wear-resistant technology, applied in the field of wear-resistant film, can solve the problem of demanding film wear resistance, achieve excellent optical stability and chemical resistance, scientific and reasonable formula, good mechanical properties.
- Summary
- Abstract
- Description
- Claims
- Application Information
AI Technical Summary
Problems solved by technology
Method used
Examples
Embodiment 1
[0023] The invention provides a technical solution: a highly wear-resistant polyurethane film, including (according to mass percentage): 33% of isophorone diisocyanate, 33% of polyethylene glycol, 6% of ethylene glycol, trimethylol Propane 2%, titanate coupling agent 0.2%, nonionic surfactant 0.8%, defoamer 0.2%, pH regulator 0.2%, flame retardant 0.5%, filler 15%, and the balance is deionized water.
[0024] A preparation method of a highly wear-resistant polyurethane film, comprising the following preparation steps:
[0025] S1: Weigh the proportion, take the material according to the above material proportion, where NCO:OH=1:1;
[0026] S2: Stirring and mixing, stir polyethylene glycol, ethylene glycol, and trimethylolpropane in the material barrel for 30 minutes, then add isophorone diisocyanate, raise the temperature to 75°C, and react for 1.5 hours, then add non-ionic Surfactants, defoamers, pH regulators, flame retardants and fillers are extruded and plasticized by an...
Embodiment 2
[0033] The invention provides a technical solution: a highly wear-resistant polyurethane film, including (according to mass percentage): 34% of isophorone diisocyanate, 32% of polyethylene glycol, 7% of ethylene glycol, trimethylol Propane 3%, titanate coupling agent 0.3%, nonionic surfactant 0.9%, defoamer 0.3%, pH regulator 0.3%, flame retardant 0.6%, filler 16%, and the balance is deionized water.
[0034] A preparation method of a highly wear-resistant polyurethane film, comprising the following preparation steps:
[0035] S1: Weigh the proportion, take the material according to the above material proportion, where NCO:OH=1:1;
[0036] S2: Stirring and mixing, stir polyethylene glycol, ethylene glycol, and trimethylolpropane in the material barrel for 35 minutes, then add isophorone diisocyanate, heat up to 75°C, and react for 1.6 hours, then add non-ionic Surfactants, defoamers, pH regulators, flame retardants and fillers are extruded and plasticized by an extruder, the...
Embodiment 3
[0043]The invention provides a technical solution: a highly wear-resistant polyurethane film, including (according to mass percentage): 34% of isophorone diisocyanate, 32% of polyethylene glycol, 8% of ethylene glycol, trimethylol Propane 4%, titanate coupling agent 0.4%, nonionic surfactant 0.9%, defoamer 0.5%, pH regulator 0.2%, flame retardant 0.7%, filler 17%, and the balance is deionized water.
[0044] A preparation method of a highly wear-resistant polyurethane film, comprising the following preparation steps:
[0045] S1: Weigh the proportion, take the material according to the above material proportion, where NCO:OH=1:1;
[0046] S2: Stirring and mixing, stir polyethylene glycol, ethylene glycol, and trimethylolpropane in the barrel for 40 minutes, then add isophorone diisocyanate, raise the temperature to 75°C, and react for 1.7 hours, then add non-ionic Surfactants, defoamers, pH regulators, flame retardants and fillers are extruded and plasticized by an extruder,...
PUM
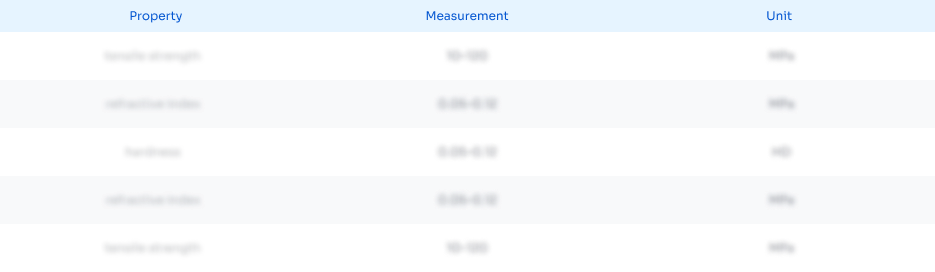
Abstract
Description
Claims
Application Information

- R&D
- Intellectual Property
- Life Sciences
- Materials
- Tech Scout
- Unparalleled Data Quality
- Higher Quality Content
- 60% Fewer Hallucinations
Browse by: Latest US Patents, China's latest patents, Technical Efficacy Thesaurus, Application Domain, Technology Topic, Popular Technical Reports.
© 2025 PatSnap. All rights reserved.Legal|Privacy policy|Modern Slavery Act Transparency Statement|Sitemap|About US| Contact US: help@patsnap.com