Robot abrasive belt grinding method and system combining active and passive force control
A robot abrasive belt and power control technology, which is applied in the direction of abrasive belt grinder, workpiece feed motion control, grinding/polishing equipment, etc. Solve the problems of passive force control and low precision of contact force control, and achieve the effects of optimizing over-underwear phenomenon, improving processing quality, and improving force control accuracy
- Summary
- Abstract
- Description
- Claims
- Application Information
AI Technical Summary
Problems solved by technology
Method used
Image
Examples
Embodiment Construction
[0050] In order to make the object, technical solution and advantages of the present invention clearer, the present invention will be further described in detail below in conjunction with the accompanying drawings and embodiments. It should be understood that the specific embodiments described here are only used to explain the present invention, not to limit the present invention. In addition, the technical features involved in the various embodiments of the present invention described below can be combined with each other as long as they do not constitute a conflict with each other.
[0051] Such as figure 1 As shown, the embodiment of the present invention provides a robot abrasive belt grinding system combined with active and passive force control, the system includes a six-axis industrial robot 1 and a corresponding abrasive belt grinding and polishing machine 3 . Among them, the end of the six-axis industrial robot 1 clamping the workpiece 5 is provided with an active fo...
PUM
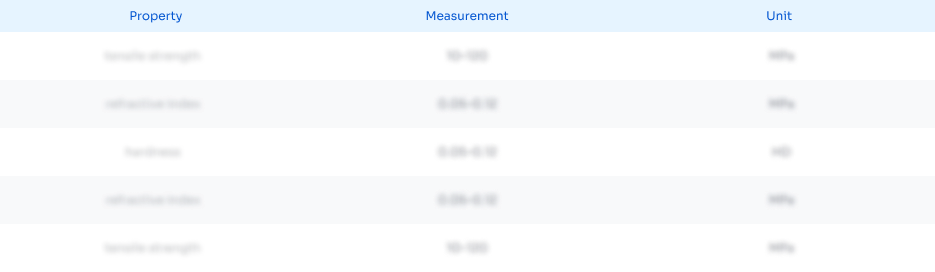
Abstract
Description
Claims
Application Information

- Generate Ideas
- Intellectual Property
- Life Sciences
- Materials
- Tech Scout
- Unparalleled Data Quality
- Higher Quality Content
- 60% Fewer Hallucinations
Browse by: Latest US Patents, China's latest patents, Technical Efficacy Thesaurus, Application Domain, Technology Topic, Popular Technical Reports.
© 2025 PatSnap. All rights reserved.Legal|Privacy policy|Modern Slavery Act Transparency Statement|Sitemap|About US| Contact US: help@patsnap.com