Collision protection method
A technology of collision object and speed direction, applied in the field of driving or reducing damage, it can solve the problems of large collision mass and large traveling speed.
- Summary
- Abstract
- Description
- Claims
- Application Information
AI Technical Summary
Problems solved by technology
Method used
Image
Examples
Embodiment Construction
[0133] In a wire electrical discharge machine (WEDM), a tool (ie, a tensioned traveling wire electrode) is guided above and below the workpiece. Basically, the upper and lower wire guides move in two parallel planes above and below the workpiece by means of X / Y and U / V axis pairs, and the vertical Z axis is used to control the two wire guides distance between pieces. The wire guide is used to precisely guide the tensioned running wire electrode. The wire guides move independently in the two planes to perform cylindrical or conical machining of the workpiece.
[0134] In general, the nomenclature of axes in machine tools is defined by ISO 841 "Industrial automation systems and integration - Numerical control of machines - Nomenclature of coordinate systems and motion", where X, Y and Z are linear axes, where Z is related to the machine's The spindle (or tool) is aligned; A, B, and C are rotational axes about X, Y, and Z, respectively; and U, V, and W are parallel linear axes ...
PUM
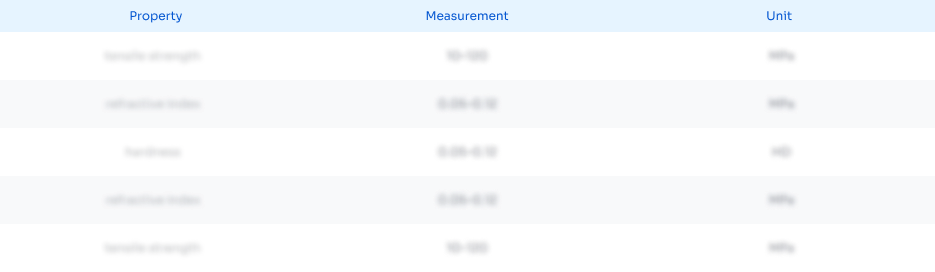
Abstract
Description
Claims
Application Information

- Generate Ideas
- Intellectual Property
- Life Sciences
- Materials
- Tech Scout
- Unparalleled Data Quality
- Higher Quality Content
- 60% Fewer Hallucinations
Browse by: Latest US Patents, China's latest patents, Technical Efficacy Thesaurus, Application Domain, Technology Topic, Popular Technical Reports.
© 2025 PatSnap. All rights reserved.Legal|Privacy policy|Modern Slavery Act Transparency Statement|Sitemap|About US| Contact US: help@patsnap.com