Preparation method of composite fireproof plate
A fireproof board, composite technology, applied in chemical instruments and methods, synthetic resin layered products, lamination and other directions, can solve the problems of low fire resistance, fragile fireproof board, difficult transportation, etc., to reduce curing shrinkage, gelatinization, etc. The effect of lowering the temperature and raising the softening point
- Summary
- Abstract
- Description
- Claims
- Application Information
AI Technical Summary
Problems solved by technology
Method used
Examples
Embodiment 1
[0031] Preparation of intermediate slabs:
[0032] Mix 70g of 100-mesh nitrile rubber powder and 400g of 200-mesh marble powder with a mass ratio of 1:3, and place them in a double-roll mixer. The temperature of the front roll is 45°C, the temperature of the rear roll is 40°C, and the roll distance is 8mm. Molding 2 times under the condition, then add 30g bentonite, 20g nano-calcium carbonate in the twin-roller mixer, mixing and masticating 2 times, discharging, extruding by extruder to obtain middle slate, for subsequent use;
[0033] Preparation of polyurethane backsheet:
[0034] In parts by weight, add 80 parts of hexamethylene diisocyanate, 30 parts of polyether diol, and 20 parts of rosin into the three-necked flask, heat up to 80°C, keep the temperature for 2 hours, cool down to 50°C, and add 10 parts of dimethylol propionic acid, 20 parts of glycerin and 20 parts of maleic anhydride, after dissolving 3 parts of dibutyltin dilaurate in 35 parts of acetone, drop them in...
Embodiment 2
[0042] Preparation of intermediate slabs:
[0043] Mix 75g of 100-mesh nitrile rubber powder and 450g of 200-mesh marble powder with a mass ratio of 1:3, and place them in a double-roller mixer. The temperature of the front roll is 50°C, the temperature of the rear roll is 45°C, and the roll distance is 9mm. Molding 2 times under the condition, then add 35g bentonite, 22g nano-calcium carbonate in the twin-roller mixer, mixing and masticating 2 times, discharging, extruding by extruder to obtain middle stone slab, for subsequent use;
[0044] Preparation of polyurethane backsheet:
[0045] In parts by weight, add 85 parts of hexamethylene diisocyanate, 35 parts of polyether diol, and 25 parts of rosin into the three-necked flask, heat up to 82°C, keep the temperature for 2.5 hours, then cool down to 55°C, and pour them into the three-necked flask in turn. Add 12 parts of dimethylolpropionic acid, 25 parts of glycerin and 22 parts of maleic anhydride, dissolve 4 parts of dibut...
Embodiment 3
[0053] Preparation of intermediate slabs:
[0054] Mix 80g of 100-mesh nitrile rubber powder and 500g of 200-mesh marble powder in a mass ratio of 1:3, and place them in a double-roll mixer. The temperature of the front roll is 55°C, the temperature of the rear roll is 50°C, and the roll distance is 10mm. masticate 3 times under the condition, then add 40g bentonite, 25g nano-calcium carbonate in the twin-roller mixer, mix and masticate 3 times, discharge, and extrude by extruder to obtain middle slate, for subsequent use;
[0055] Preparation of polyurethane backsheet:
[0056] In parts by weight, add 90 parts of hexamethylene diisocyanate, 40 parts of polyether diol, and 30 parts of rosin into the three-necked flask, heat up to 85°C, keep the temperature for 3 hours, cool down to 60°C, and add 15 parts of dimethylolpropionic acid, 30 parts of glycerin and 25 parts of maleic anhydride, after dissolving 5 parts of dibutyltin dilaurate in 40 parts of acetone, drop them in at a...
PUM
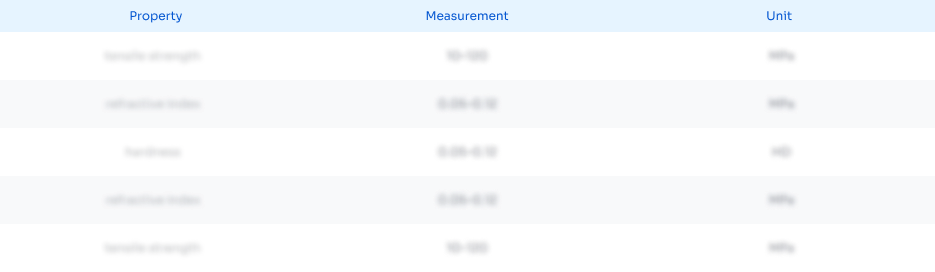
Abstract
Description
Claims
Application Information

- R&D Engineer
- R&D Manager
- IP Professional
- Industry Leading Data Capabilities
- Powerful AI technology
- Patent DNA Extraction
Browse by: Latest US Patents, China's latest patents, Technical Efficacy Thesaurus, Application Domain, Technology Topic, Popular Technical Reports.
© 2024 PatSnap. All rights reserved.Legal|Privacy policy|Modern Slavery Act Transparency Statement|Sitemap|About US| Contact US: help@patsnap.com