Coreless spinning machining method for large-scale multi-variable-diameter hollow shaft
A processing method and hollow shaft technology, applied in the field of spinning, can solve the problems of difficult processing of multiple variable diameter hollow shafts, low reduction of machining allowances, poor forming quality, etc., so as to eliminate the uneven force on the workpiece. , reduce processing costs and achieve the effect of light weight
- Summary
- Abstract
- Description
- Claims
- Application Information
AI Technical Summary
Problems solved by technology
Method used
Image
Examples
Embodiment 1
[0049] Such as figure 1 Shown is the hollow shaft 100 that needs to be processed and formed in this embodiment, including a hollow body section 110. One end of the body section 110 is a thin-diameter section 120 with a significantly reduced inner diameter. The thin-diameter section 120 extends for a certain length, and the thin-diameter section 120 and the main body section 110 have a plurality of reduced-diameter sections with gradually increasing outer diameter transitions, specifically including the first reduced-diameter section 121 and the second reduced-diameter section 122 extending from the thin-diameter section 120 to the main body section 110 in sequence and the third diameter reduction section 123, each diameter reduction section is an arc-shaped smooth transition section, and a straight extension section is connected between each diameter reduction section, and a step surface distribution is formed as a whole between each diameter reduction section, specifically as ...
Embodiment 2
[0063] The coreless spinning processing method of a large-scale multiple-diameter hollow shaft in this embodiment is basically the same as that in Embodiment 1. Furthermore, the vertical spinning system used in this embodiment includes The lower mold unit 500, and the rotary wheel installation unit 700 arranged on both sides of the lower mold unit 500, such as figure 2 As shown, an upper mold unit 600 is also arranged above the lower mold unit 500, wherein a coarse rotary wheel 200 and a shaping rotary wheel 400 are installed on the rotary wheel installation unit 700 on one side, and a rotary wheel installation unit 700 on the other side is installed with The positions of the fine turning wheel 300 and the shaping wheel 400, the rough turning wheel 200 and the fine turning wheel 300 are corresponding, and the positions of the shaping wheels 400 on both sides are corresponding. When in use, the workpiece is clamped in the lower mold unit 500 and the lower mold unit 500 drives ...
Embodiment 3
[0067] The coreless spinning processing method of a large-scale multiple-diameter hollow shaft in this embodiment is basically the same as the above-mentioned embodiment 2, and further, as Figure 8 As shown, the spinning wheel installation unit 700 in this embodiment includes a stand seat 701, and the upper and lower ends of the stand seat 701 are respectively provided with mounting plates 702, and the spinning wheel is arranged between the mounting plates 702 at both ends. Specifically, A wheel shaft 710 is arranged between the mounting plates 702 at both ends, and the ends of the wheel shaft 710 pass through the mounting plate 702 and are fastened by nuts at both ends. The middle part of 710 is provided with a wheel seat 720, and the bottom of the wheel seat 720 is provided with a circle of supporting ring segments along the axial direction. Bolts are used to fasten the spinning wheel on the supporting ring segment. The outer side of the wheel seat 720 is also provided wit...
PUM
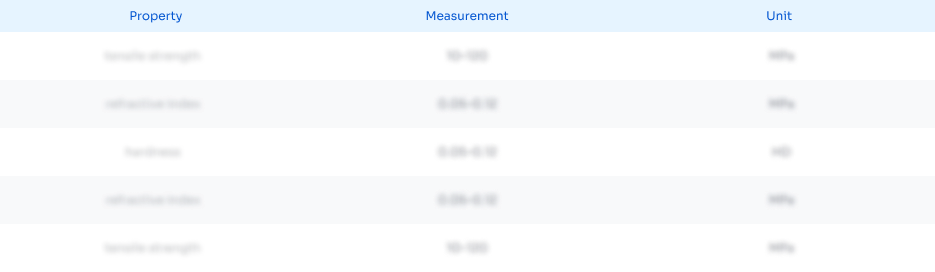
Abstract
Description
Claims
Application Information

- R&D Engineer
- R&D Manager
- IP Professional
- Industry Leading Data Capabilities
- Powerful AI technology
- Patent DNA Extraction
Browse by: Latest US Patents, China's latest patents, Technical Efficacy Thesaurus, Application Domain, Technology Topic, Popular Technical Reports.
© 2024 PatSnap. All rights reserved.Legal|Privacy policy|Modern Slavery Act Transparency Statement|Sitemap|About US| Contact US: help@patsnap.com