A kind of preparation method of whitening foaming agent
A technology of foaming agent and stabilizer, which is applied in the preparation of whitening foaming agent, whitening foaming agent for polyvinyl chloride and its preparation field, which can solve the problem of unstable production quality of downstream product manufacturers and increase the amount of stabilizer , the decline in mechanical properties of the product, etc., to avoid insufficient gas generation, avoid severe corrosion, and improve grinding efficiency
- Summary
- Abstract
- Description
- Claims
- Application Information
AI Technical Summary
Problems solved by technology
Method used
Examples
Embodiment 1
[0052] A preparation method of whitening foaming agent, comprising the following steps:
[0053] S1, the preparation of semi-finished product A:
[0054] S11. Put the sodium bicarbonate and the composite calcium-zinc stabilizer into a high-speed mixer and stir evenly, and the mixing temperature does not exceed 80°C;
[0055] S12, sending the mixed material in step S11 into a jet mill, and performing jet milling to obtain modified ultrafine sodium bicarbonate, i.e. semi-finished product A;
[0056] S2, the preparation of semi-finished product B:
[0057] S21. After uniformly mixing the citrate and citric acid, send them into a jet mill for jet milling to obtain a powder with a median particle size of 5-25um;
[0058] S22, adding the powder obtained in step S21 into a high mixer, dissolving fatty acid and its derivatives with a low-boiling point organic solvent to obtain a solution of fatty acid and its derivatives; then spraying the solution of fatty acids and its derivatives...
Embodiment 2
[0078] A preparation method of whitening foaming agent, comprising the following steps:
[0079] S1, the preparation of semi-finished product A:
[0080] S11. Put the sodium bicarbonate and the composite calcium-zinc stabilizer into a high-speed mixer and stir evenly, and the mixing temperature does not exceed 80°C;
[0081] S12, sending the mixed material in step S11 into a jet mill, and performing jet milling to obtain modified ultrafine sodium bicarbonate, i.e. semi-finished product A;
[0082] S2, the preparation of semi-finished product B:
[0083] S21, after citrate and citric acid are mixed uniformly, send into jet mill, carry out jet pulverization, obtain the powder body that median particle size is 25um;
[0084] S22, adding the powder obtained in step S21 into a high mixer, dissolving fatty acid and its derivatives with a low-boiling point organic solvent to obtain a solution of fatty acid and its derivatives; then spraying the solution of fatty acids and its deriv...
Embodiment 3
[0104] A preparation method of whitening foaming agent, comprising the following steps:
[0105] S1, the preparation of semi-finished product A:
[0106] S11. Put the sodium bicarbonate and the composite calcium-zinc stabilizer into a high-speed mixer and stir evenly, and the mixing temperature does not exceed 80°C;
[0107] S12, sending the mixed material in step S11 into a jet mill, and performing jet milling to obtain modified ultrafine sodium bicarbonate, i.e. semi-finished product A;
[0108] S2, the preparation of semi-finished product B:
[0109] S21, after citrate and citric acid are mixed uniformly, send into jet mill, carry out jet pulverization, obtain the powder body that median particle diameter is 5um;
[0110] S22, adding the powder obtained in step S21 into a high mixer, dissolving fatty acid and its derivatives with a low-boiling point organic solvent to obtain a solution of fatty acid and its derivatives; then spraying the solution of fatty acids and its de...
PUM
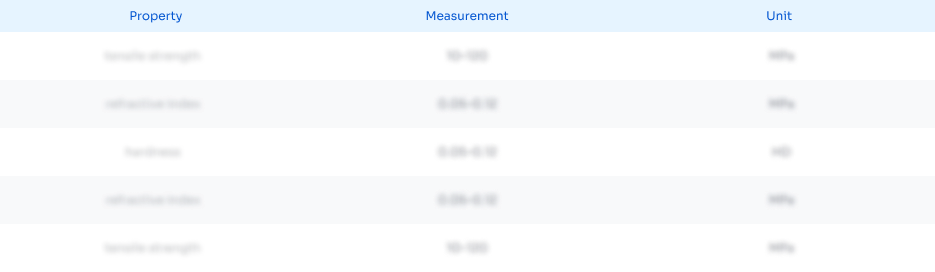
Abstract
Description
Claims
Application Information

- R&D
- Intellectual Property
- Life Sciences
- Materials
- Tech Scout
- Unparalleled Data Quality
- Higher Quality Content
- 60% Fewer Hallucinations
Browse by: Latest US Patents, China's latest patents, Technical Efficacy Thesaurus, Application Domain, Technology Topic, Popular Technical Reports.
© 2025 PatSnap. All rights reserved.Legal|Privacy policy|Modern Slavery Act Transparency Statement|Sitemap|About US| Contact US: help@patsnap.com