Flexible welding robot system and welding method thereof
A welding robot and welding method technology, applied in welding accessories, manipulators, program-controlled manipulators, etc., can solve problems such as inconvenient use and physical injury of workers, improve product quality and production efficiency, save labor costs, and improve welding efficiency Effect
- Summary
- Abstract
- Description
- Claims
- Application Information
AI Technical Summary
Problems solved by technology
Method used
Image
Examples
Embodiment Construction
[0071] The present invention will be described in detail below in conjunction with the accompanying drawings and specific embodiments, where the schematic embodiments and descriptions of the present invention are used to explain the present invention, but not to limit the present invention.
[0072] Such as figure 1 , figure 2 As shown, a flexible welding robot system of the present invention includes: a global vision unit, a flexible welding robot unit, a flexible detection robot unit, a master control unit and a workbench unit; wherein,
[0073] The global vision unit comprises a global vision assembly 3 and a global vision assembly fixing frame 4 fixed on the ceiling, the global vision assembly 3 is fixed at the bottom of the global vision assembly fixing frame 4, and the global vision assembly 3 is provided with a multifunctional welding workbench 7 below the global vision assembly 3. The functional welding workbench 7 is provided with a workpiece 13 to be welded clamped...
PUM
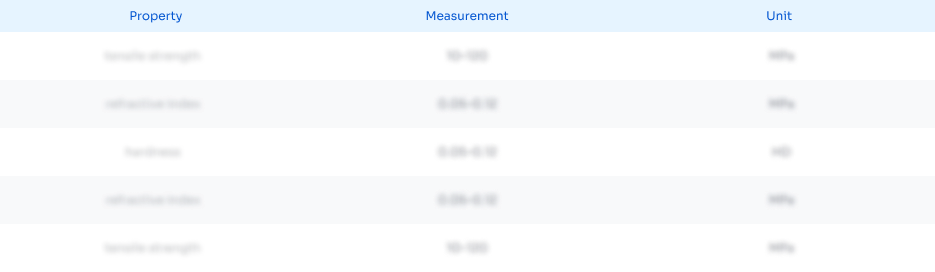
Abstract
Description
Claims
Application Information

- Generate Ideas
- Intellectual Property
- Life Sciences
- Materials
- Tech Scout
- Unparalleled Data Quality
- Higher Quality Content
- 60% Fewer Hallucinations
Browse by: Latest US Patents, China's latest patents, Technical Efficacy Thesaurus, Application Domain, Technology Topic, Popular Technical Reports.
© 2025 PatSnap. All rights reserved.Legal|Privacy policy|Modern Slavery Act Transparency Statement|Sitemap|About US| Contact US: help@patsnap.com