Manufacturing method of trench type double-layer gate MOSFET
A manufacturing method and double-layer gate technology, applied in semiconductor/solid-state device manufacturing, electrical components, semiconductor devices, etc., can solve problems that affect the stability of the first contact hole, cannot guarantee complete filling, and affect product quality. Shape stability, process cost reduction, and product quality improvement
- Summary
- Abstract
- Description
- Claims
- Application Information
AI Technical Summary
Problems solved by technology
Method used
Image
Examples
Embodiment Construction
[0080] Such as image 3 As shown, it is a flow chart of the manufacturing method of the trench type double-layer gate MOSFET according to the embodiment of the present invention; as shown in Fig. 4A to Figure 4H Shown is a schematic diagram of the device structure in each step of the method of the embodiment of the present invention; the manufacturing method of the trench type double-layer gate MOSFET of the embodiment of the present invention includes the following steps:
[0081] Step 1, such as Figure 4A As shown, a plurality of trenches are formed on the semiconductor substrate 1 by photolithography definition plus etching process, the trenches include a plurality of gate trenches 2a and at least one source extraction trench 2b, and the gate trenches 2a are formed In the device unit area, the source extraction trench 2b is located outside the device unit area, the source extraction trench 2b communicates with each of the gate trenches 2a, and the source extraction trenc...
PUM
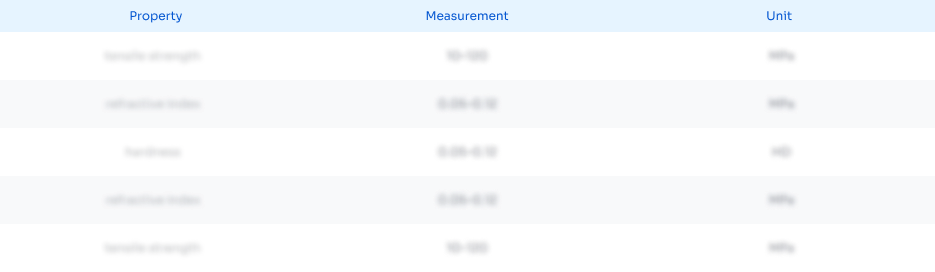
Abstract
Description
Claims
Application Information

- R&D
- Intellectual Property
- Life Sciences
- Materials
- Tech Scout
- Unparalleled Data Quality
- Higher Quality Content
- 60% Fewer Hallucinations
Browse by: Latest US Patents, China's latest patents, Technical Efficacy Thesaurus, Application Domain, Technology Topic, Popular Technical Reports.
© 2025 PatSnap. All rights reserved.Legal|Privacy policy|Modern Slavery Act Transparency Statement|Sitemap|About US| Contact US: help@patsnap.com