LED optical strip and method of manufacturing the same
A technology for light-emitting diodes and a manufacturing method, which is applied in the fields of semiconductor/solid-state device manufacturing, electrical components, and electric-solid-state devices, etc., can solve the problems of increased cost, increased weight and size of light-emitting diode light bars, complicated manufacturing process procedures, etc. The effect of process cost
- Summary
- Abstract
- Description
- Claims
- Application Information
AI Technical Summary
Problems solved by technology
Method used
Image
Examples
Embodiment Construction
[0021] The invention discloses a light emitting diode light bar and a manufacturing method thereof. In order to make the narration of the present invention more detailed and complete, refer to the following description and cooperate Figure 1 to Figure 6 .
[0022] Please refer to Figure 1 to Figure 6 , which is a schematic diagram of the manufacturing process of a light emitting diode light strip according to a preferred embodiment of the present invention, wherein Figure 1 to Figure 4 is a cross-sectional diagram, Figure 5 and Figure 6 It is a schematic diagram from above. In an exemplary embodiment, making a Figure 6 In the case of the LED light bar 112 shown, a circuit board 100 may be provided first for chips to be disposed thereon, wherein the circuit board 100 is preferably pre-set with a required circuit layout. In one embodiment, the circuit board 100 can be a common printed circuit board. Next, using, for example, a bonding method, a plurality of LED chips ...
PUM
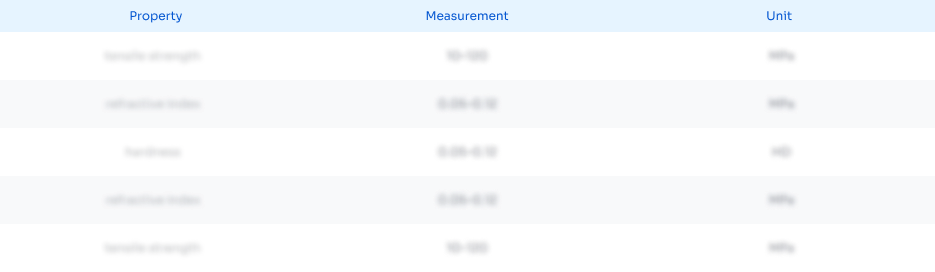
Abstract
Description
Claims
Application Information

- Generate Ideas
- Intellectual Property
- Life Sciences
- Materials
- Tech Scout
- Unparalleled Data Quality
- Higher Quality Content
- 60% Fewer Hallucinations
Browse by: Latest US Patents, China's latest patents, Technical Efficacy Thesaurus, Application Domain, Technology Topic, Popular Technical Reports.
© 2025 PatSnap. All rights reserved.Legal|Privacy policy|Modern Slavery Act Transparency Statement|Sitemap|About US| Contact US: help@patsnap.com