Preparation method of metal oxide loaded monatomic catalyst
A metal compound and catalyst technology, applied in the field of materials science and engineering, can solve the problems of high cost, low preparation amount, large carrier loss, etc., and achieve the effects of reducing cost and difficulty, wide application, and preventing agglomeration
- Summary
- Abstract
- Description
- Claims
- Application Information
AI Technical Summary
Problems solved by technology
Method used
Image
Examples
Embodiment 1
[0032] Mix 0.004 g of tetraammine platinum nitrate and 1 g of iron oxide into a commercial 50 ml agate ball mill jar with a cover, and add 10 3 mm agate beads and 80 6 mm agate beads to it. Put the ball mill jar into the planetary ball mill QM3SP4L, set the ball milling conditions to rotate clockwise and counterclockwise alternately every 1.5 h, the two-way stop waiting time is 0, the frequency is 30 HZ, and the ball milling is 24 hours. Stopped for two or three times in the middle, took out the ball mill tank and stirred it with a plastic spoon, loosened the compacted oxide carrier, and continued to run. The ball-milled solid was put into a porcelain boat, and calcined in a muffle furnace or tube furnace at 400 °C in air for 2 h to obtain the corresponding single-atom catalyst material. Spherically aberration corrected TEM such as figure 1 Pt / Fe 2 o 3 shown.
Embodiment 2
[0034] Mix 0.0017 g of platinum oxide and 1 g of manganese oxide into a commercial 50 ml agate ball mill jar with a lid, and add 10 3 mm agate beads and 80 6 mm agate beads to it. Put the ball mill jar into the planetary ball mill QM3SP4L, set the ball milling conditions to rotate clockwise and counterclockwise alternately every 1.5 h, the two-way stop waiting time is 0, the frequency is 30 HZ, and the ball milling is 24 hours. Stopped for two or three times in the middle, took out the ball mill tank and stirred it with a plastic spoon, loosened the compacted oxide carrier, and continued to run. The ball-milled solid was put into a porcelain boat, and calcined in a muffle furnace or tube furnace at 400 °C in air for 2 h to obtain the corresponding single-atom catalyst material.
Embodiment 3
[0036] Mix 0.125 g of tetraammine palladium nitrate and 25 g of iron oxide and add it to a commercial 250 ml agate ball mill jar with a cover, and add 10 3 mm agate beads and 80 6 mm agate beads to it. Put the ball mill jar into the planetary ball mill QM3SP4L, set the ball milling conditions to rotate clockwise and counterclockwise alternately every 1.5 h, the two-way stop waiting time is 0, the frequency is 30 HZ, and the ball milling is 48 hours. Stopped for two or three times in the middle, took out the ball mill tank and stirred it with a plastic spoon, loosened the compacted oxide carrier, and continued to run. The ball-milled solid was put into a porcelain boat, and calcined in a muffle furnace or tube furnace at 600 °C in air for 2 h to obtain the corresponding single-atom catalyst material. Spherically aberration corrected TEM such as figure 2 PD 1 / Fe 2 o 3 shown.
PUM
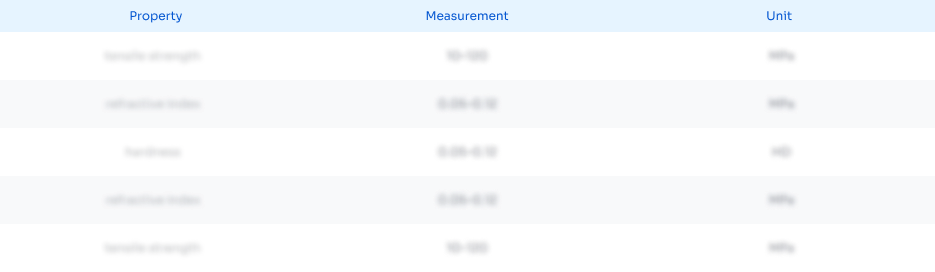
Abstract
Description
Claims
Application Information

- Generate Ideas
- Intellectual Property
- Life Sciences
- Materials
- Tech Scout
- Unparalleled Data Quality
- Higher Quality Content
- 60% Fewer Hallucinations
Browse by: Latest US Patents, China's latest patents, Technical Efficacy Thesaurus, Application Domain, Technology Topic, Popular Technical Reports.
© 2025 PatSnap. All rights reserved.Legal|Privacy policy|Modern Slavery Act Transparency Statement|Sitemap|About US| Contact US: help@patsnap.com