Organic waste liquid gasification furnace and waste gas treatment process
A technology of organic waste liquid and gasifier, applied in incinerators, chemical instruments and methods, combustion methods, etc., can solve problems such as nozzle fouling and equipment corrosion, and achieve system balance and stability, large contact area, and volume Increased effect
- Summary
- Abstract
- Description
- Claims
- Application Information
AI Technical Summary
Problems solved by technology
Method used
Image
Examples
Embodiment 1
[0036] refer to figure 1 , an organic waste liquid gasification furnace, comprising a furnace body 100 and a gasification chamber 110 inside the furnace body 100, the furnace body 100 is provided with an air inlet channel 120 and an air outlet channel communicating with the gasification chamber 110 150, the outer side of the furnace body 100 is provided with a waste liquid storage tank 200 for storing waste liquid, and the waste liquid storage tank 200 is connected with the waste liquid outlet at the bottom of the gasification chamber 110, and a mist atomization nozzle 130, the atomization nozzle 130 atomizes the waste liquid in the waste liquid storage tank 200 and then sprays it into the furnace body 100; The organic volatiles and the hot air are blown out from the outlet channel 150 along with the organic volatiles, and the incompletely vaporized waste liquid flows back into the waste liquid storage tank 200 .
[0037]The hot air can evaporate the volatile matter in the or...
Embodiment 2
[0049] This embodiment proposes a method for reducing hot air consumption during the process of hot air blowing out from the air outlet channel 150. Specifically, the bottom surface of the gasification chamber 110 is a conical surface, and the air outlet channel 150 and the air inlet channel 120 set in the vertical direction.
[0050] When the volatile matter driven by the hot air flows in the vertical air inlet passage 120, the contact area with the inner wall of the passage is small, and the volatile matter is not easy to adhere to the pipe wall, and the hot air is sprayed vertically downward from the air inlet passage 120 to the gasification In the chamber 110, it flows along the conical bottom surface of the gasification chamber 110. If the bottom surface is a plane, the hot air blowing on the plane will have a greater reaction force, and the hot air will disperse to both sides, while the conical bottom surface can guide The flow of hot air, the hot air entering from the a...
Embodiment 3
[0053] This embodiment proposes a method for controlling the volatile matter concentration and temperature in the air outlet channel 150: refer to Figure 5 The inner wall of the air outlet channel 150 is provided with a VOC concentration monitor 180 for detecting the concentration of volatile components and a thermocouple 190 for detecting the temperature, and the air intake volume of the hot air is adjusted according to the detected temperature and concentration. The flow rate of hot air blown into the gasification chamber 110 is controlled by the hot air regulating valve. When the VOC concentration detected by the VOC concentration monitor 180 is low, the system automatically opens the hot air regulating valve to increase the air volume of the hot air intake, thereby improving the gasification rate. The temperature in the chamber 110 increases the vaporization rate of volatile matter; similarly, when the VOC concentration detected by the VOC concentration monitor 180 is too ...
PUM
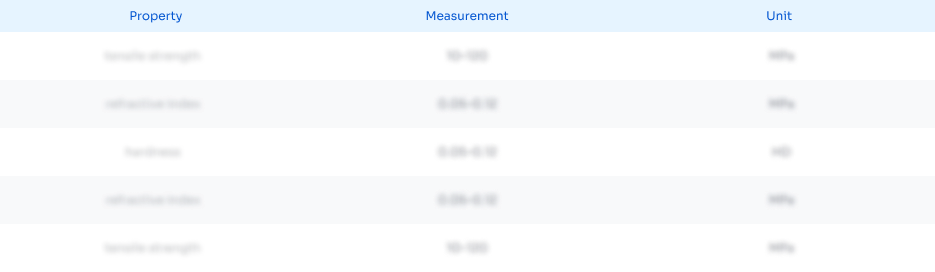
Abstract
Description
Claims
Application Information

- Generate Ideas
- Intellectual Property
- Life Sciences
- Materials
- Tech Scout
- Unparalleled Data Quality
- Higher Quality Content
- 60% Fewer Hallucinations
Browse by: Latest US Patents, China's latest patents, Technical Efficacy Thesaurus, Application Domain, Technology Topic, Popular Technical Reports.
© 2025 PatSnap. All rights reserved.Legal|Privacy policy|Modern Slavery Act Transparency Statement|Sitemap|About US| Contact US: help@patsnap.com