Flexible drive rigidity-variable differential coupling robot finger device
A robot finger and flexible drive technology, applied in the field of robotics, can solve problems such as poor reliability and excessive energy loss, and achieve the effects of reducing heat transfer jams, increasing rated carrying capacity, and improving robustness
- Summary
- Abstract
- Description
- Claims
- Application Information
AI Technical Summary
Problems solved by technology
Method used
Image
Examples
Embodiment Construction
[0047]The technical solution of the present invention will be further described below in conjunction with the embodiments and accompanying drawings, but it is not limited thereto. Any modification or equivalent replacement of the technical solution of the present invention without departing from the spirit and scope of the technical solution of the present invention should cover In the protection scope of the present invention.
[0048] This embodiment provides a flexible driving stiffness variable differential coupling robot finger device, such as Figure 1-8 As shown, the robotic finger device includes a base 1, a first knuckle 2, a second knuckle 3, a first joint shaft 4, a second joint shaft 5, a first flexible drive with self-locking, a second belt There is a self-locking flexible driver, the first transmission wheel 811, the second transmission wheel 813, the third transmission wheel 821, the fourth transmission wheel 823, the first transmission member 812, the second tr...
PUM
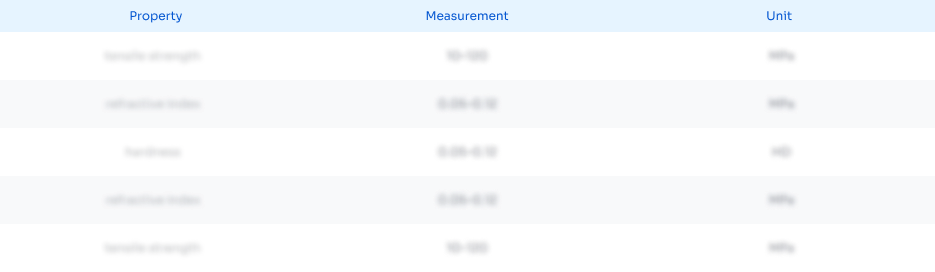
Abstract
Description
Claims
Application Information

- R&D
- Intellectual Property
- Life Sciences
- Materials
- Tech Scout
- Unparalleled Data Quality
- Higher Quality Content
- 60% Fewer Hallucinations
Browse by: Latest US Patents, China's latest patents, Technical Efficacy Thesaurus, Application Domain, Technology Topic, Popular Technical Reports.
© 2025 PatSnap. All rights reserved.Legal|Privacy policy|Modern Slavery Act Transparency Statement|Sitemap|About US| Contact US: help@patsnap.com