Transparent heat-resistant polycarbonate material and preparation method thereof
A polycarbonate and heat-resistant technology, which is applied in the field of polycarbonate composites and its preparation, can solve problems such as poor solubility, poor processing performance, high melt viscosity, and poor fluidity, and achieve improved light transmission performance and industrial preparation. Simple, compatibility-enhancing effects
- Summary
- Abstract
- Description
- Claims
- Application Information
AI Technical Summary
Problems solved by technology
Method used
Image
Examples
Embodiment 2-1
[0035] Step (1). Vacuum dry the polycarbonate and polyarylate at 120°C for 24 hours respectively (Li-TFSI does not need to be dried);
[0036] Step (2). Add 36g of dried polycarbonate, 24g of dried polyarylate and 0.3g of Li-TFSI into the internal mixer, melt and blend at 260°C, and melt and mix at 50rpm / min 10min.
[0037]Step (3). The mixture is discharged from the melting and kneading equipment and lowered to normal temperature to obtain a polycarbonate composite material.
[0038] The mass ratio of polycarbonate, polyarylate and Li-TFSI in the polycarbonate composite prepared in Example 2-1 is 60:40:0.5.
[0039] The materials prepared in Comparative Example 1 and Example 2-1 were tested for thermal performance.
[0040] The materials prepared in Comparative Example 1 and Example 2-1 were subjected to a light transmittance-haze test, and the test conditions were as follows: the samples should be pressed into 0.3 mm thin slices.
[0041] The glass transition temperature ...
Embodiment 2-2
[0050] Step (1). Vacuum dry the polycarbonate and polyarylate at 120°C for 24 hours respectively (Li-TFSI does not need to be dried);
[0051] Step (2). Add 42g of dried polycarbonate, 18g of dried polyarylate and 0.3g of Li-TFSI into the internal mixer, melt and blend at 260°C, and melt and mix at 50rpm / min 10min.
[0052] Step (3). The mixture is discharged from the melting and kneading equipment and lowered to normal temperature to obtain a polycarbonate compound with high transparency.
[0053] The mass ratio of polycarbonate, polyarylate and Li-TFSI in the polycarbonate compound prepared in Example 2-2 is 70:30:0.5.
Embodiment 2-3
[0055] Step (1). Vacuum dry the polycarbonate and polyarylate at 120°C for 24 hours respectively (Li-TFSI does not need to be dried);
[0056] Step (2). Add 48g of dried polycarbonate, 16g of dried polyarylate and 0.3g of Li-TFSI into the internal mixer, melt and blend at 250°C, and melt and mix at 40rpm / min 10min.
[0057] Step (3). The mixture is discharged from the melting and kneading equipment and lowered to normal temperature to obtain a polycarbonate compound with high transparency.
[0058] The mass ratio of polycarbonate, polyarylate and Li-TFSI in the polycarbonate composite prepared in Example 2-3 is 80:20:0.5.
PUM
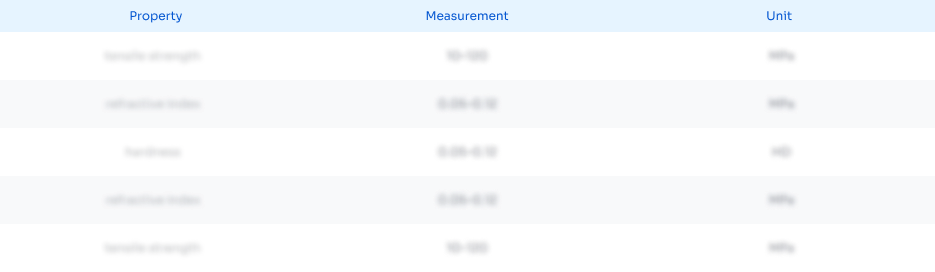
Abstract
Description
Claims
Application Information

- R&D
- Intellectual Property
- Life Sciences
- Materials
- Tech Scout
- Unparalleled Data Quality
- Higher Quality Content
- 60% Fewer Hallucinations
Browse by: Latest US Patents, China's latest patents, Technical Efficacy Thesaurus, Application Domain, Technology Topic, Popular Technical Reports.
© 2025 PatSnap. All rights reserved.Legal|Privacy policy|Modern Slavery Act Transparency Statement|Sitemap|About US| Contact US: help@patsnap.com