High-performance Al4SiC4 fiber and preparation process thereof
A preparation process and high-performance technology, applied in the field of fiber preparation, can solve the problems of high cost and difficulty in industrialized preparation of fibers, and achieve the effects of high melting point, overcoming difficulty in preparation and low thermal expansion coefficient.
- Summary
- Abstract
- Description
- Claims
- Application Information
AI Technical Summary
Problems solved by technology
Method used
Image
Examples
Embodiment 1
[0026] a) molding, mixing bauxite and silica according to the ratio of 65% by weight: 20% and then putting them into a molding machine, controlling the molding particle size to be 30mm-50mm, and forming mixture A after compression molding;
[0027] b) batching, according to the weight ratio of mixture A and carbonaceous reducing agent is 1:0.20, carbonaceous reducing agent is added to the mixture, after mixing to form mixture B, said carbonaceous reducing agent is coke and charcoal with a weight ratio of 1 : Mixed at a ratio of 1.5.
[0028] Such as Figure 1-2 As shown, the following steps are also included:
[0029] c) Melting reduction, put the mixture B into the melting furnace 1, and in the state of nitrogen or argon closed oxygen barrier, control the temperature to be 1700°C-2200°C for melting, and form a molten liquid after melting, and flow into the heat preservation container 2 , and then flow out from the nozzle 7 of the heat preservation container, the temperature...
Embodiment 2
[0034] a) Forming, mixing bauxite and silica according to the ratio of 80% by weight: 35% and then putting it into a molding machine, controlling the molding particle size to be 30mm-50mm, and forming a mixture A after pressing;
[0035] b) batching, according to the weight ratio of mixture A and carbonaceous reducing agent is 1:0.35, carbonaceous reducing agent is added to the mixture, after mixing to form mixture B, said carbonaceous reducing agent is coke and charcoal with a weight ratio of 1 : 2 ratio mixed.
[0036] Such as Figure 1-2 As shown, the following steps are also included:
[0037] c) Melting reduction, put the mixture B into the melting furnace 1, and in the state of nitrogen or argon closed oxygen barrier, control the temperature to be 1700°C-2200°C for melting, and form a molten liquid after melting, and flow into the heat preservation container 2 , and then flow out from the nozzle 7 of the heat preservation container, the temperature of the molten liquid...
Embodiment 3
[0042] a) molding, mixing bauxite and silica according to the ratio of 70% by weight: 28% and then putting them into a molding machine, controlling the molding particle size to be 30mm-50mm, and forming a mixture A after compression molding;
[0043] b) batching, according to the weight ratio of mixture A and carbonaceous reducing agent is 1:0.50, carbonaceous reducing agent is added to the mixture, after mixing to form mixture B, said carbonaceous reducing agent is composed of coke and carbon in a weight ratio of 3 : Mixed at a ratio of 2.2.
[0044] Such as Figure 1-2 As shown, the following steps are also included:
[0045] c) Melting reduction, put the mixture B into an ultra-high temperature pyrolysis gasification reduction melting furnace, in the state of nitrogen or argon sealing oxygen, control the temperature at 1700°C-2100°C for melting, and form a molten liquid after melting , flows into the insulation container 2, and then flows out from the nozzle 7 of the insu...
PUM
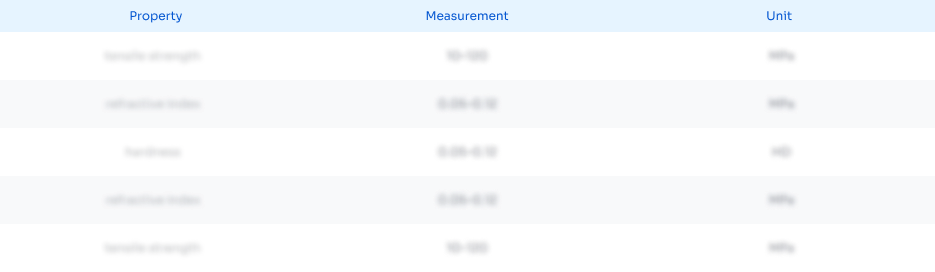
Abstract
Description
Claims
Application Information

- Generate Ideas
- Intellectual Property
- Life Sciences
- Materials
- Tech Scout
- Unparalleled Data Quality
- Higher Quality Content
- 60% Fewer Hallucinations
Browse by: Latest US Patents, China's latest patents, Technical Efficacy Thesaurus, Application Domain, Technology Topic, Popular Technical Reports.
© 2025 PatSnap. All rights reserved.Legal|Privacy policy|Modern Slavery Act Transparency Statement|Sitemap|About US| Contact US: help@patsnap.com