A fully automatic welding machine control system
A control system, fully automatic technology, applied in welding equipment, manufacturing tools, welding equipment, etc., can solve problems such as unreasonable processing technology and process, inability to complete can processing and welding processing, etc., to achieve good processing efficiency, improve The effect of processing efficiency
- Summary
- Abstract
- Description
- Claims
- Application Information
AI Technical Summary
Problems solved by technology
Method used
Image
Examples
Embodiment 1
[0046] A fully automatic welding machine control system, comprising a rolling device 1, a transfer assembly 2 arranged at one end of the rolling device 1, and a tank body welding device 3 arranged at the other end of the transfer assembly 2; the rolling device 1 is provided with The drum assembly 4, the transmission assembly 2 is provided with a transmission belt 5 on the upper end surface, the tank body welding device 3 has a slide assembly 26, and the center axis of the drum assembly 4, transmission belt 5, and slide assembly 26 along the length direction On the same straight line, the end of the drum assembly 4 is in close contact with one end of the transmission belt 5, and the other end of the transmission belt 5 is in close contact with one end of the slide assembly 26; The devices are connected in sequence, and the metal plate is sequentially processed by the rolling device, the transfer assembly, and the tank welding device to complete the tank body processing at one ti...
Embodiment 2
[0048]On the basis of Embodiment 1, the rolling device 1 includes a machine tool body 7, a transmission assembly 8 arranged at one end of the body 7, and the roller assembly 4 is arranged above the body 7; the transmission assembly 8 includes a power motor 9, The gear assembly 10 meshingly connected with the power motor 9, the first rotating main shaft 43 connected with the drum assembly 4, and the second rotating main shaft 11, the first rotating main shaft 43 is provided with a hydraulic lift assembly 12, and the gear assembly 10 includes an outer casing The power gear 13 on the main shaft of the power motor 9, the first transmission gear 14 meshed with the power gear 13, the transmission gear set 15 meshed with the first transmission gear 14, and the second transmission gear 44 meshed with the transmission gear set 15 , the second transmission gear 44 and the first transmission gear 14 are fixedly connected with the first rotating main shaft 43 and the second rotating main s...
Embodiment 3
[0050] On the basis of Embodiment 2, the transmission gear set 15 is hinged with the main body through the rotating main shaft 16 fixedly connected to the center of the transmission gear set 15, and the first rotating main shaft 43 is provided with a bearing on the outer sleeve of the hinged end of the main body, so The above-mentioned bearing is fixedly connected with the body; by setting two meshing gears in the transmission gear set, the power transmission to the first transmission gear is realized and at the same time, the rotation direction of the second transmission gear is opposite to that of the first transmission gear, so that the metal plate enters the first transmission gear. The metal plate behind the gap between the roller and the second roller can enter between the first roller and the second roller under the action of the friction between the first roller and the second roller, and wrap around the outer wall of the first roller to form a Cylindrical.
PUM
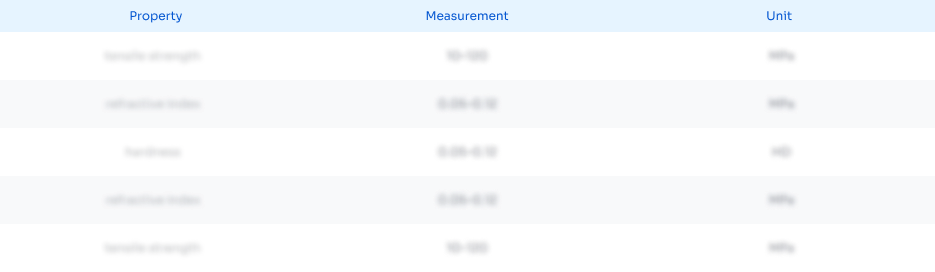
Abstract
Description
Claims
Application Information

- R&D Engineer
- R&D Manager
- IP Professional
- Industry Leading Data Capabilities
- Powerful AI technology
- Patent DNA Extraction
Browse by: Latest US Patents, China's latest patents, Technical Efficacy Thesaurus, Application Domain, Technology Topic, Popular Technical Reports.
© 2024 PatSnap. All rights reserved.Legal|Privacy policy|Modern Slavery Act Transparency Statement|Sitemap|About US| Contact US: help@patsnap.com