A method of heat -solving power generation and comprehensive utilization of rice shells
A technology of pyrolysis, rice husk, applied in the direction of nanotechnology, adhesive type, aldehyde/ketone condensation polymer adhesive, etc. for materials and surface science, which can solve the loss of heat, waste of energy, inability to process, etc. problems, to achieve the effect of increasing energy density, avoiding waste water generation, and saving energy consumption
- Summary
- Abstract
- Description
- Claims
- Application Information
AI Technical Summary
Problems solved by technology
Method used
Examples
Embodiment 1
[0052] The method for power generation and comprehensive utilization of rice husk pyrolysis specifically includes the following steps:
[0053] Step 1. Rice husk pyrolysis
[0054] Select rice husks, screen and purify them and add them to the pyrolysis tower through the bucket elevator, and then enter the drying zone, pyrolysis zone, oxygen removal and decoking zone, and cooling zone in sequence, so that the temperature of the pyrolysis section is kept at 650 ° C, and the pyrolysis is 0.5 hours. Rice husk is decomposed into pyrolysis gas and pyrolysis carbon;
[0055] Step 2. Deoxygenation and coke-rich phenol
[0056] The 650°C pyrolysis gas and pyrolysis charcoal obtained in the step 1 continue to descend along the pyrolysis tower, and maintain a constant temperature to remove oxygen and decoke for 0.5 hours to obtain anaerobic pyrolysis gas and pyrolysis charcoal, and eliminate the Oxygen, so that the pyrolysis gas and pyrolysis carbon are in an oxygen-free state in the f...
Embodiment 2
[0068] 1. Pyrolytic carbon cooling
[0069] The pyrolytic charcoal in Step 2 of Example 1 continues to descend into the indirect water-cooled cooling section of the pyrolysis tower tubes, cools down to 250°C, and falls to the bottom of the pyrolysis tower, and is sent into the sealed storage bin through the screw propeller; water-cooled and cooled to form The high-temperature water vapor is directly introduced into the tar steam reforming furnace;
[0070] 2. Preparation of nano-silica
[0071] Transfer the remaining solid obtained in Step 5 of Example 1 to the reactor, add a hydrochloric acid solution with a concentration of 5wt% according to the solid-to-liquid ratio of 1Kg: 5L, heat up to 120°C, seal the reaction for 30min, cool down, filter, and separate the filtrate and filter cake ; The filter cake was washed to neutral, dried, pulverized and dispersed to prepare silica / carbon powder; and then heat-treated at 600°C to prepare a high-purity nano-silica powder with a puri...
Embodiment 3
[0074] The phenol-rich wastewater in Step 3 and Step 5 in Example 1 was combined, and the total phenol content was calibrated to be 32wt%. According to the weight ratio of formaldehyde to phenol is 1:2, and sodium hydroxide is 6% of the mass of phenol, phenol-rich wastewater and sodium hydroxide are added to the reaction kettle, and when the temperature rises to 50°C, the concentration of the first batch is 37 wt%. formaldehyde solution (accounting for 80% of the total formaldehyde solution), and react at a constant temperature of 60°C for 1h. Raise the temperature to 80°C, add the remaining formaldehyde solution, and react at a constant temperature at 80°C for 2 hours, then cool the system down to 45°C-50°C, stop the reaction, and dehydrate the obtained phenolic resin under reduced pressure at 65°C until the viscosity reaches 600mPa·s , discharging, and preparing a biomass phenol-based adhesive.
PUM
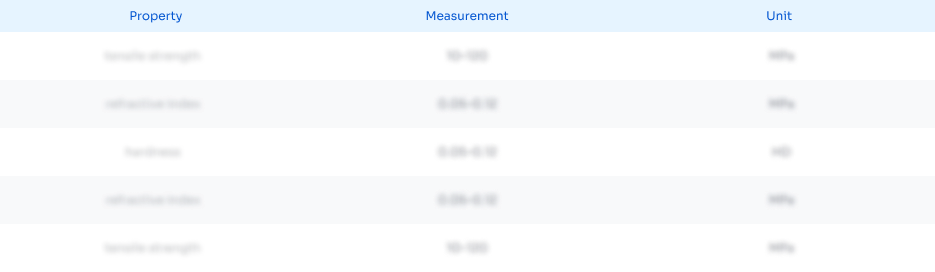
Abstract
Description
Claims
Application Information

- Generate Ideas
- Intellectual Property
- Life Sciences
- Materials
- Tech Scout
- Unparalleled Data Quality
- Higher Quality Content
- 60% Fewer Hallucinations
Browse by: Latest US Patents, China's latest patents, Technical Efficacy Thesaurus, Application Domain, Technology Topic, Popular Technical Reports.
© 2025 PatSnap. All rights reserved.Legal|Privacy policy|Modern Slavery Act Transparency Statement|Sitemap|About US| Contact US: help@patsnap.com