Screening method of 3D printing powder
A 3D printing and powder technology, applied in the field of 3D printing, can solve the problems of incomplete powder sintering, substandard performance of printed parts, affecting the thickness of powder coating, etc., and achieve the effect of reducing humidity and increasing oxygen content
- Summary
- Abstract
- Description
- Claims
- Application Information
AI Technical Summary
Problems solved by technology
Method used
Examples
Embodiment 1
[0025] Put the powder collection tank containing the TA1 powder prepared by gas atomization upside down on the feed port of the air classifier, vacuumize the air classifier, pass argon, and then start the air classifier for the first screening, and control the air flow The impeller speed of the classifier is 2000prm, and the air intake volume is 1500m 3 / h; After the first screening, the obtained TA1 powder with a particle size of 15-250 μm is passed into the glove box for secondary screening. Then start the ultrasonic sieving machine for sieving, control the ultrasonic frequency to 15KHz, and sieve for 20 minutes. After the second sieving is completed, TA1 printing powder with a particle size of 15-45 μm is obtained; finally, TA1 is packed in the glove box with an inflatable packaging machine. The printing powder is packaged in a cylindrical nylon vacuum bag.
Embodiment 2
[0027] Put the powder collection tank containing the TC4 powder prepared by gas atomization upside down on the feed port of the air classifier, vacuumize the air classifier, pass argon, and then start the air classifier for the first screening, and control the air flow The impeller speed of the classifier is 1800prm, and the air intake volume is 1300m 3 / h; After the first screening, the obtained TC4 powder with a particle size of 15-250 μm is passed into the glove box for secondary screening. Then start the ultrasonic sieving machine for sieving, control the ultrasonic frequency to 18KHz, and sieve for 15 minutes. The second sieving is completed to obtain TC4 printing powder with a particle size in the range of 15-45 μm; finally, use an inflatable packaging machine in the glove box to pack TC4 The printing powder is packaged in a cylindrical nylon vacuum bag.
Embodiment 3
[0029] Put the powder collection tank containing the TC21 powder prepared by gas atomization upside down at the feed port of the air classifier, vacuumize the air classifier, pass argon, and then start the air classifier for the first screening to control the air flow The impeller speed of the classifier is 1600prm, and the air intake volume is 1000m 3 / h; After the first screening, the obtained TC21 powder with a particle size of 15-250 μm is passed into the glove box for secondary screening. Then start the ultrasonic sieving machine for sieving, control the ultrasonic frequency to 20KHz, and sieve for 10 minutes. After the second sieving is completed, TC21 printing powder with a particle size of 15-45 μm is obtained; finally, use an inflatable packaging machine in the glove box to pack TC21 The printing powder is packaged in a cylindrical nylon vacuum bag.
PUM
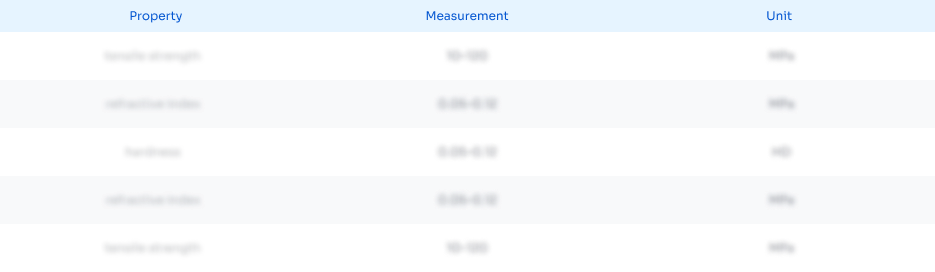
Abstract
Description
Claims
Application Information

- R&D
- Intellectual Property
- Life Sciences
- Materials
- Tech Scout
- Unparalleled Data Quality
- Higher Quality Content
- 60% Fewer Hallucinations
Browse by: Latest US Patents, China's latest patents, Technical Efficacy Thesaurus, Application Domain, Technology Topic, Popular Technical Reports.
© 2025 PatSnap. All rights reserved.Legal|Privacy policy|Modern Slavery Act Transparency Statement|Sitemap|About US| Contact US: help@patsnap.com