Thermal fatigue testing device
A test device, thermal fatigue technology, applied in the direction of measuring devices, greenhouse gas reduction, instruments, etc., can solve the problems of uneven air injection of samples, cumbersome experimental operations, different cooling speeds, etc., and achieve improved reliability and uniform air injection angle Effect
- Summary
- Abstract
- Description
- Claims
- Application Information
AI Technical Summary
Problems solved by technology
Method used
Image
Examples
Embodiment 1
[0028] When the number of tests is small and the experimental samples need to be removed for observation every few heating cycles, in order to facilitate repeated sampling operations, it is possible to directly spray protective gas on the samples through the ventilation coil without using a vacuum cover. The anti-oxidation protection of the sample avoids the trouble of repeated vacuuming. The specific process is as follows. The commonly used aluminum alloy die-casting mold steel SKD 61 is used as the test sample, and the test sample is fixed in the heating coil with the upper and lower thimbles, and the test sample is placed in the center of the heating coil by adjusting the positions of the upper and lower thimbles. Open the inlet valve, inject protective gas (nitrogen or argon) through the inlet of the gas cooling part, and maintain the low-pressure injection state, and create a local protective gas atmosphere around the test sample inside the heating coil. Then energize th...
Embodiment 2
[0030] For the case where the number of tests is large and repeated sampling is not required for observation, it is recommended to use a vacuum cover to protect the sample from oxidation. The specific process is as follows: take SKD 61, a commonly used aluminum alloy die-casting mold steel, as the test sample, fix the test sample in the heating coil with the upper and lower thimbles, and place the test sample in the heating coil by adjusting the position of the upper and lower thimbles. right in the middle. Close the intake valve and exhaust valve, open the exhaust valve and vacuum system, pump the air in the vacuum cover to a vacuum state, and close the exhaust valve and vacuum system. Open the intake valve, fill the protective gas (nitrogen or argon) through the intake port of the gas cooling part until the pressure in the vacuum cover reaches 1 atmosphere, then open the exhaust valve, and energize the heating coil for heating for 5s. The test sample was heated up to 650°C,...
PUM
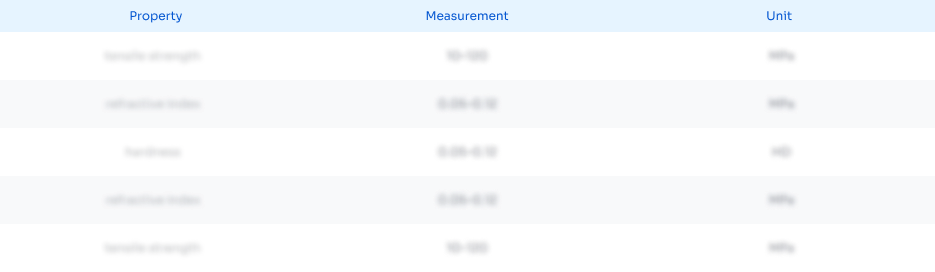
Abstract
Description
Claims
Application Information

- Generate Ideas
- Intellectual Property
- Life Sciences
- Materials
- Tech Scout
- Unparalleled Data Quality
- Higher Quality Content
- 60% Fewer Hallucinations
Browse by: Latest US Patents, China's latest patents, Technical Efficacy Thesaurus, Application Domain, Technology Topic, Popular Technical Reports.
© 2025 PatSnap. All rights reserved.Legal|Privacy policy|Modern Slavery Act Transparency Statement|Sitemap|About US| Contact US: help@patsnap.com