Nanometer modified plant fiber spun filament
A nano-modified, plant fiber technology, applied in the field of spinning materials, can solve the problems of non-degradable environment of chemical synthetic fiber bristles, natural bristles easily breed bacteria, difficult to clean, etc., and achieve sufficient raw material sources, enhanced adsorption, and improved degradation. effect of speed
- Summary
- Abstract
- Description
- Claims
- Application Information
AI Technical Summary
Problems solved by technology
Method used
Image
Examples
Embodiment 1
[0046] Embodiment 1: Preparation of nano-modified plant cellulose
[0047] (1) Enzymolysis: Cut natural plant fiber materials (jute, loofah or other natural fiber materials) into fibers with a length of 0.5~3cm, cook them in an electric heating constant temperature water bath, and stir them magnetically for 30 minutes. After the stirring is completed, filter them with suction , and dried in an oven at 105±3°C to obtain dried natural plant fibers. Enzymolyze with a compound enzyme composed of pectinase: laccase: hemicellulase, and enzymolyze at a temperature of 55±3°C for 12 hours to obtain enzymatically hydrolyzed plant fibers. The ratio of pectinase: laccase: hemicellulase in the compound enzyme is 1:2:2, and the amount of compound enzyme added is 5% of the mass of natural plant fiber material.
[0048] (2) Dissolution: Inactivate the natural plant fiber after enzymolysis at 95°C for 10 minutes, then filter the plate and frame, wash the filter residue and dry it at 50±3°C fo...
Embodiment 2
[0054] Embodiment 2: Preparation of nano-modified plant cellulose
[0055] (1) Enzymolysis: Cut natural plant fiber materials (jute, loofah or other natural fiber materials) into fibers with a length of 0.5~3cm, cook them in an electric heating constant temperature water bath, and stir them magnetically for 30 minutes. After the stirring is completed, filter them with suction , and dried in an oven at 110±3°C to obtain dried natural plant fibers. Use pectinase: laccase: hemicellulase compound enzyme to enzymolyze, and enzymolyze for 10 h at a temperature of 45±3°C to obtain enzymatically hydrolyzed plant fibers; in the compound enzyme, pectinase: laccase : The ratio of hemicellulase is 1:0.5:0.5, and the amount of compound enzyme added is 8% of the mass of natural plant fiber material.
[0056] (2) Dissolution: Inactivate the natural plant fiber after enzymolysis at 95°C for 10 minutes, then filter the plate and frame, wash the filter residue and dry it at 50°C~60°C for 5 hou...
Embodiment 3
[0061] Embodiment 3: the preparation of nano-modified plant cellulose
[0062] (1) Enzymolysis: Cut natural plant fiber materials (jute, loofah or other natural fiber materials) into fibers with a length of 0.5~3cm, cook them in an electric heating constant temperature water bath, and stir them magnetically for 30 minutes. After the stirring is completed, filter them with suction , and dried in an oven at 110±3°C to obtain dried natural plant fibers. Use pectinase: laccase: hemicellulase to enzymolyze the compound enzyme, and enzymolyze it for 24 hours at a temperature of 50±3°C to obtain the enzymatically hydrolyzed plant fiber; in the compound enzyme, pectinase: laccase : The ratio of hemicellulase is 1:0.5:0.5, and the amount of compound enzyme added is 1% of the mass of natural plant fiber material.
[0063] (2) Dissolution: Inactivate the natural plant fiber after enzymolysis at 95°C for 10 minutes, then filter the plate and frame, wash the filter residue and dry it at 5...
PUM
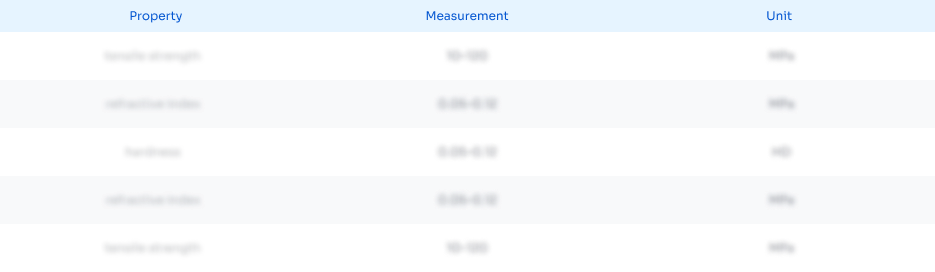
Abstract
Description
Claims
Application Information

- R&D
- Intellectual Property
- Life Sciences
- Materials
- Tech Scout
- Unparalleled Data Quality
- Higher Quality Content
- 60% Fewer Hallucinations
Browse by: Latest US Patents, China's latest patents, Technical Efficacy Thesaurus, Application Domain, Technology Topic, Popular Technical Reports.
© 2025 PatSnap. All rights reserved.Legal|Privacy policy|Modern Slavery Act Transparency Statement|Sitemap|About US| Contact US: help@patsnap.com