Production method for improving grain size of 6063 aluminum alloy center matrix
A production method and a technology of grain size, applied in the production field of improving the grain size of the central matrix of 6063 aluminum alloy, can solve problems such as uneven product performance, product deformation, and coarse grain size, so as to reduce the trend of grain growth, Avoid the growth of grains and reduce the effect of grain size
- Summary
- Abstract
- Description
- Claims
- Application Information
AI Technical Summary
Problems solved by technology
Method used
Image
Examples
Embodiment 1
[0028] A. Melting and casting: first put pure aluminum into the furnace to melt, and when heated to 700°C, add 1.5% aluminum titanium boron wire after melting, of which the titanium content is 5% and other trace elements.
[0029] B. Stirring: Mix the ingredients in the melt evenly by stirring, and the stirring time is 30 minutes.
[0030] C. Cast rod homogenization treatment: the cast rod is cast from the melt, and the temperature of the cast rod is kept at 575° C. for 8 hours by using the homogenization treatment process.
[0031] D. Extruded aluminum rod temperature: the temperature of the cast rod is controlled at 480°C before extrusion, and the outlet temperature of the cast rod is ensured at 520°C.
[0032] E. Mold design: by changing the R angle 1 at the feed inlet, the radius of R angle 1 is 8mm, the working zone 2 after R angle 1 is 3.5mm, and the depth 3 of the feed inlet of the mold is 25mm
[0033] F. Extrusion speed: In order to promote the metal to enter the coo...
Embodiment 2
[0036] A. Melting and casting: first put pure aluminum into the furnace to melt, and when heated to 720°C, add 1% aluminum titanium boron wire after melting, of which the titanium content is 5% and other trace elements.
[0037] B. Stirring: Mix the ingredients in the melt evenly by stirring, and the stirring time is 30 minutes.
[0038] C. Cast rod homogenization treatment: Cast rods through melt casting, use the homogenization treatment process to make the temperature of the casting rods 580° C. and keep it warm for 8 hours.
[0039] D. Extruded aluminum rod temperature: the temperature of the cast rod is controlled at 475°C before extrusion, and the outlet temperature of the cast rod is ensured at 530°C.
[0040] E. Mold design: by changing the R angle 1 at the feed inlet, the radius of R angle 1 is 8mm, the working zone 2 after R angle 1 is 3.5mm, and the depth 3 of the feed inlet of the mold is 25mm
[0041] F. Extrusion speed: In order to promote the metal to enter the ...
Embodiment 3
[0044] A. Melting and casting: first put pure aluminum into the furnace to melt, and when heated to 750°C, add 1.3% aluminum titanium boron wire after melting, of which the titanium content is 5% and other trace elements.
[0045] B. Stirring: Mix the ingredients in the melt evenly by stirring, and the stirring time is 40 minutes.
[0046] C. Cast rod homogenization treatment: the cast rod is cast from the melt, and the temperature of the cast rod is kept at 585° C. for 9 hours by using the homogenization treatment process.
[0047] D. Extruded aluminum rod temperature: the temperature of the cast rod is controlled at 470°C before extrusion, and the outlet temperature of the cast rod is kept at 540°C.
[0048] E. Mold design: By changing the R angle 1 at the feed inlet, the radius of R angle 1 is 8mm, the working zone 2 after R angle 1 is 3.5mm, and the depth 3 of the feed inlet of the mold is 25mm.
[0049] F. Extrusion speed: In order to promote the metal to enter the cooli...
PUM
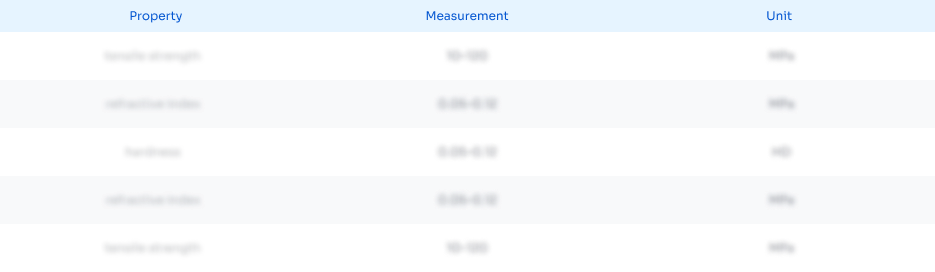
Abstract
Description
Claims
Application Information

- R&D
- Intellectual Property
- Life Sciences
- Materials
- Tech Scout
- Unparalleled Data Quality
- Higher Quality Content
- 60% Fewer Hallucinations
Browse by: Latest US Patents, China's latest patents, Technical Efficacy Thesaurus, Application Domain, Technology Topic, Popular Technical Reports.
© 2025 PatSnap. All rights reserved.Legal|Privacy policy|Modern Slavery Act Transparency Statement|Sitemap|About US| Contact US: help@patsnap.com