A kind of magnesium gel material, preparation method and application for preparing glass magnesium plate
A gel material and magnesia technology, applied in the field of magnesia gel material, preparation, and preparation of glass magnesium plate, can solve the problems of poor water resistance, cracking, easy to warp, etc., to improve water resistance, compact internal structure, long-term Stable performance
- Summary
- Abstract
- Description
- Claims
- Application Information
AI Technical Summary
Problems solved by technology
Method used
Examples
preparation example Construction
[0028] The preparation process of the phenolic resin foamed glass magnesium flat plate of the present invention, at first determines the quality of each raw material according to the density, size and quality of the prepared board; Keep warm at 50~70°C for 2~4h, add magnesia cement slurry and mix; enter the board making stage, which mainly includes laying mesh cloth, setting thickness and molding, etc. Remove the mold, and then maintain under natural conditions until the moisture content meets the requirements, generally the moisture content is less than 8%, and the glass magnesium plate is obtained.
[0029] During the preparation process of the glass magnesium flat plate of the present invention, the foaming temperature of the phenolic resin is preferably 70°C.
Embodiment 1
[0032] In this example, a white plate of 2440mm×1220mm×15mm is produced, the density of the plate is 900kg / m³, the total mass of the plate is about 40.2kg, and the ratio of raw materials is as follows:
[0033] Magnesium oxide 11.75kg, magnesium chloride 7.05kg, water 10.575kg, filler heavy calcium powder 5.875kg, phenolic resin 4.7kg, blowing agent n-pentane 0.132kg, catalyst phosphoric acid 0.47kg, PP fiber 0.235kg. The quality of foamed phenolic resin accounts for 15.7% of the quality of magnesia cement in the present embodiment.
[0034] Mix magnesia, magnesium chloride, and water to form magnesia cement slurry, mix phenolic resin, foaming agent, catalyst and toughening agent, keep warm at 70°C for 2 hours, add magnesia cement slurry and mix; lay grid cloth 1. Preliminary curing at 55°C for 24 hours after the thickness setting and forming, demoulding, and then curing under natural conditions until the moisture content is less than 8%, and the glass magnesium plate required...
Embodiment 2
[0037] In this example, a red plate of 2440mm×1220mm×15mm is produced, the density of the plate is 600kg / m³, the total mass of the plate is about 26.8kg, and the ratio of raw materials is as follows:
[0038] Magnesium oxide 7.875kg, magnesium chloride 4.725kg, water 7.1kg, filler heavy calcium powder 3.94kg, phenolic resin 3.15kg, blowing agent n-pentane 0.22kg, catalyst phosphoric acid 0.315kg, glass fiber 0.235kg, iron oxide red pigment 0.13kg . The quality of foamed phenolic resin accounts for 16.58% of the quality of magnesia cement in the present embodiment.
[0039] The preparation process of the glass magnesium plate of this embodiment is the same as that of Embodiment 1. The performance test of the glass magnesium flat plate prepared in this embodiment is shown in Table 1.
PUM
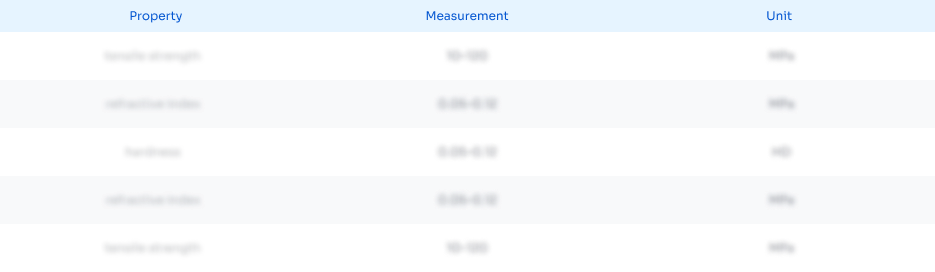
Abstract
Description
Claims
Application Information

- R&D
- Intellectual Property
- Life Sciences
- Materials
- Tech Scout
- Unparalleled Data Quality
- Higher Quality Content
- 60% Fewer Hallucinations
Browse by: Latest US Patents, China's latest patents, Technical Efficacy Thesaurus, Application Domain, Technology Topic, Popular Technical Reports.
© 2025 PatSnap. All rights reserved.Legal|Privacy policy|Modern Slavery Act Transparency Statement|Sitemap|About US| Contact US: help@patsnap.com