A kind of welding waveform control method of nickel-based alloy gas metal arc welding
A technology for melting electrode gas and nickel-based alloys, applied in welding equipment, welding accessories, manufacturing tools, etc., can solve the problems of poor welding effect, incomplete droplet transfer, difficult droplet transfer, etc., and achieve high deposition efficiency, Low cost, realize the effect of all-position welding
- Summary
- Abstract
- Description
- Claims
- Application Information
AI Technical Summary
Problems solved by technology
Method used
Image
Examples
Embodiment 1
[0048] In the S-P-GMAW welding method, welding current control is the core technology to suppress spatter. Such as Figure 4 As shown, the present invention provides a preferred embodiment of a welding waveform control method for gas metal arc welding of nickel-based alloys. The specific control period corresponds to the welding process.
[0049] Figure 4 Stage A is the base value stage (corresponding to image 3 -a): Set the welding voltage to 20V, the welding current to 35A, and the duration t 1 Set it to 8ms to maintain stable combustion of arc 3;
[0050] Figure 4 Middle B stage is the early stage of pulse stage (corresponding to image 3 -b): Set welding voltage to 43V, welding current to 480A, duration t 2 Set it to 0.9ms, so that the welding wire 2 melts rapidly, and the droplet 1 grows rapidly;
[0051] Figure 4 Middle C stage is the late stage of pulse stage (corresponding to image 3 -c): Set welding voltage to 44V, welding current to 520A, duration t 3...
Embodiment 2
[0057] Such as Figure 5 As shown, another preferred embodiment of the method for controlling the welding waveform of a nickel-based alloy gas shielded metal arc welding provided by the present invention. The specific control period corresponds to the welding process.
[0058] Figure 5 Stage A is the base value stage (corresponding to image 3 -a): Set welding voltage to 21V, welding current to 40A, duration t 1 Set it to 7.5ms to maintain stable combustion of arc 3;
[0059] Figure 5 Middle B stage is the early stage of pulse stage (corresponding to image 3 -b): Set welding voltage to 41V, welding current to 460A, duration t 2 Set it to 1.0ms, so that the welding wire 2 melts rapidly, and the droplet 1 grows rapidly;
[0060] Figure 5 Middle C stage is the late stage of pulse stage (corresponding to image 3 -c): Set welding voltage to 46V, welding current to 540A, duration t 3 Set to 1.3ms, so that the droplet is elongated and necked;
[0061] Figure 5 The m...
PUM
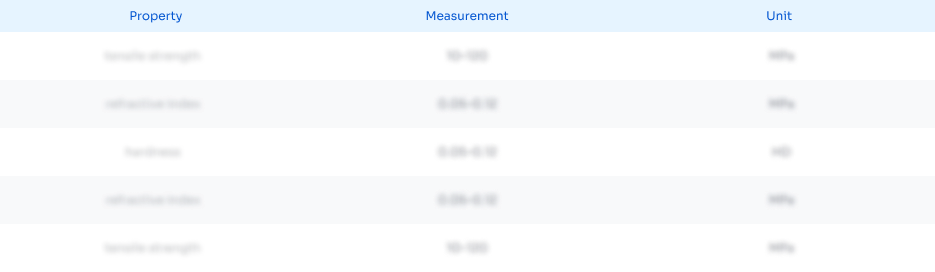
Abstract
Description
Claims
Application Information

- R&D
- Intellectual Property
- Life Sciences
- Materials
- Tech Scout
- Unparalleled Data Quality
- Higher Quality Content
- 60% Fewer Hallucinations
Browse by: Latest US Patents, China's latest patents, Technical Efficacy Thesaurus, Application Domain, Technology Topic, Popular Technical Reports.
© 2025 PatSnap. All rights reserved.Legal|Privacy policy|Modern Slavery Act Transparency Statement|Sitemap|About US| Contact US: help@patsnap.com