Preparation method of in-situ growth graphene composite carbon material of graphite sheet
A graphene composite and in-situ growth technology, which is applied in the field of high thermal conductivity materials and composite carbon materials, can solve the problems of reducing the performance of composite reinforcements, easy agglomeration of carbon nanotubes, and difficult growth direction of carbon nanotubes. The effect of simple process
- Summary
- Abstract
- Description
- Claims
- Application Information
AI Technical Summary
Problems solved by technology
Method used
Image
Examples
Embodiment 1
[0027] This embodiment provides a method for preparing a graphene composite carbon material grown in situ on a graphite sheet, comprising the following steps:
[0028] 1) Surface treatment of natural graphite flakes: Wash and dry the natural graphite flakes with a diameter of 500 μm in absolute ethanol, acetone and deionized water respectively.
[0029] 2) High-temperature surface treatment of natural graphite flakes: the natural graphite flakes were heated to 800°C at a rate of 15°C / min in an ambient atmosphere of 400sccm argon and 300sccm hydrogen, and kept for 10 minutes to further remove impurities and reduce the surface.
[0030] 3) GNP growth: 20sccm methane gas was introduced to provide the carbon source required for growth. At this time, the flow rate of hydrogen was 500sccm, and the flow rate of argon was 100sccm. This process was maintained for 6h.
[0031] In the present embodiment, the test of graphite flake in-situ growth graphene composite carbon material graphen...
Embodiment 2
[0034] This embodiment provides a method for preparing a graphene composite carbon material grown in situ on a graphite sheet, comprising the following steps:
[0035] 1) Surface treatment of natural graphite flakes: the natural graphite flakes with a graphite flake diameter of 700 μm were washed and dried in absolute ethanol, acetone and deionized water respectively.
[0036] 2) High-temperature surface treatment of natural graphite flakes: the natural graphite flakes were heated up to 800°C at a rate of 5°C / min in an atmosphere of 400sccm argon and 200sccm hydrogen and held for 10 minutes to further remove impurities and reduce the surface.
[0037] 3) GNP growth: 30 sccm methane gas was introduced to provide the carbon source required for growth. At this time, the flow rate of hydrogen was 100 sccm, and the flow rate of argon was 500 sccm. This process was maintained for 6 hours.
[0038] In the present embodiment, the test of graphene growth ratio of graphite flake in situ...
Embodiment 3
[0041] This embodiment provides a method for preparing a graphene composite carbon material grown in situ on a graphite sheet, comprising the following steps:
[0042] 1) Surface treatment of natural graphite flakes: Wash and dry the natural graphite flakes with a diameter of 1000 μm in absolute ethanol, acetone and deionized water respectively.
[0043] 2) High-temperature surface treatment of natural graphite flakes: the natural graphite flakes were heated to 1000°C at a rate of 20°C / min in an ambient atmosphere of 500sccm argon and 500sccm hydrogen and kept for 60min to further remove impurities and reduce the surface.
[0044] 3) GNP growth: 100 sccm of methane gas was introduced to provide the carbon source required for growth. At this time, the flow rate of hydrogen was 500 sccm, and the flow rate of argon was 500 sccm. This process was maintained for 16 hours.
[0045] In the present embodiment, the test of graphite flake in-situ growth graphene composite carbon materia...
PUM
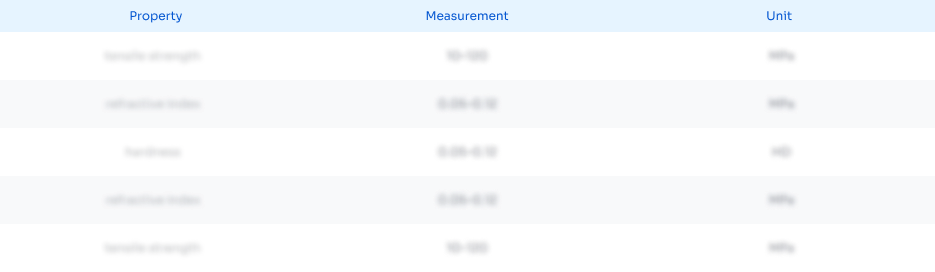
Abstract
Description
Claims
Application Information

- R&D
- Intellectual Property
- Life Sciences
- Materials
- Tech Scout
- Unparalleled Data Quality
- Higher Quality Content
- 60% Fewer Hallucinations
Browse by: Latest US Patents, China's latest patents, Technical Efficacy Thesaurus, Application Domain, Technology Topic, Popular Technical Reports.
© 2025 PatSnap. All rights reserved.Legal|Privacy policy|Modern Slavery Act Transparency Statement|Sitemap|About US| Contact US: help@patsnap.com