Rotary machine intelligent fault diagnosis method based on integrated depth auto-encoder
A technology of deep self-encoding and rotating machinery, which is applied to the automatic fault diagnosis of rotating machinery. Based on the field of intelligent fault diagnosis of rotating machinery based on integrated deep self-encoder, it can solve the problems of classification accuracy, low generalization ability and low robustness. And other issues
- Summary
- Abstract
- Description
- Claims
- Application Information
AI Technical Summary
Problems solved by technology
Method used
Image
Examples
Embodiment Construction
[0045] Below in conjunction with accompanying drawing and specific embodiment, the present invention is described in further detail:
[0046] refer to figure 1 , the present invention comprises the following steps:
[0047] Step 1) Get the training dataset X 1 and the test dataset X 2 .
[0048] The present invention can be used for intelligent fault diagnosis of rotating machinery such as rolling bearings and gearboxes. In this embodiment, rolling bearings are taken as an example, and the bearing fault data of Case Western Reserve University is used for experimental analysis. A total of 12 fault types of rolling bearings are collected through the data acquisition system. , 3600 vibration time-domain signals as a data set. details as follows:
[0049] The vibration time-domain signals used in this embodiment are all from the bearing data set of Case Western Reserve University in the United States. The test bearing mainly includes four fault types: normal state, ball defe...
PUM
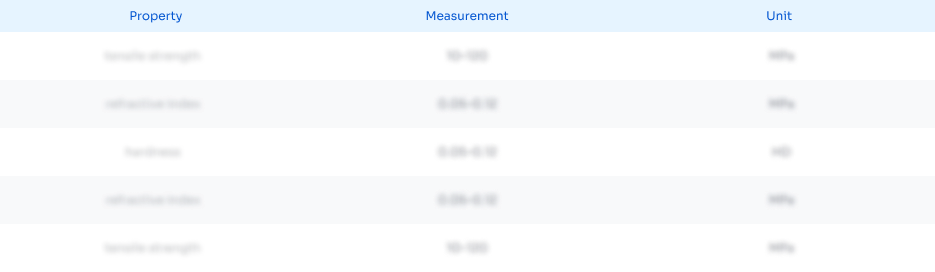
Abstract
Description
Claims
Application Information

- R&D
- Intellectual Property
- Life Sciences
- Materials
- Tech Scout
- Unparalleled Data Quality
- Higher Quality Content
- 60% Fewer Hallucinations
Browse by: Latest US Patents, China's latest patents, Technical Efficacy Thesaurus, Application Domain, Technology Topic, Popular Technical Reports.
© 2025 PatSnap. All rights reserved.Legal|Privacy policy|Modern Slavery Act Transparency Statement|Sitemap|About US| Contact US: help@patsnap.com