A preparation method of pervaporation layer-by-layer assembly membrane for gasoline desulfurization
A technology of pervaporation membrane and layer-by-layer assembly, which is applied in the fields of dialysis purification, chemical instruments and methods, and semi-permeable membrane separation, etc. Problems such as the increase of molecular mass transfer resistance, to achieve the effect of improving structure and performance stability, good industrial application prospects, and strong adsorption selection ability
- Summary
- Abstract
- Description
- Claims
- Application Information
AI Technical Summary
Problems solved by technology
Method used
Image
Examples
Embodiment 1
[0023] 1) Preparation of porous bottom membrane: mix polymer bottom membrane material PVDF, inorganic particle zinc nitrate, and solvent triethyl phosphate, stir at 90°C for 2 hours until the membrane liquid is uniform, and then place it in a vacuum oven for defoaming to obtain inorganic Particle / polymer film liquid; the mass ratio of polymer base film material, inorganic particles, and solvent is 100:0.5:300; the obtained film liquid is coated with a scraping film on polyester non-woven fabric, and water is used as a gel bath , using the immersion precipitation phase inversion method to make the membrane, so that the solvent and water in the membrane liquid can be exchanged thoroughly;
[0024]2) In-situ preparation of MOFs membrane: dissolve the organic ligand 2-methylimidazole and the metal salt zinc nitrate in the solvent methanol, mix well, and immerse the bottom membrane prepared in step 1) into the organic ligand and metal salt 10s in the mixed solution, the temperature...
Embodiment 2
[0028] 1) Preparation of porous bottom membrane: mix polymer bottom membrane material PEI, inorganic particle zinc nitrate, and solvent N-methylpyrrolidone, stir at 80°C for 12 hours until the membrane liquid is uniform, and then place it in a vacuum oven for degassing to obtain Inorganic particles / polymer film liquid; the mass ratio of polymer bottom film material, inorganic particles, and solvent is 100:5:500; the obtained film liquid is coated with scraping film on polyester non-woven fabric, and water is used as gel Bath, the membrane is prepared by the immersion precipitation phase inversion method, so that the solvent and water in the membrane liquid can be exchanged thoroughly;
[0029] 2) In-situ preparation of MOFs membrane: Dissolve the organic ligand benzimidazole and the metal salt zinc nitrate in the solvent ethanol, mix well, and immerse the bottom membrane prepared in step 1) into the mixture containing the organic ligand and the metal salt. In the solution for ...
Embodiment 3
[0033] 1) Preparation of porous bottom membrane: Mix the polymer bottom membrane material CA, inorganic particle zinc hydroxide, and solvent N,N-dimethylformamide, stir at 70°C for 24h, until the membrane liquid is uniform, and then place in a vacuum The inorganic particles / polymer film liquid is obtained by degassing in an oven; the mass ratio of the polymer bottom film material, inorganic particles, and solvent is 100:70:1300; the obtained film liquid is coated with a scraping film on a polyester non-woven fabric, Using water as the gel bath, the membrane is prepared by the immersion precipitation phase inversion method, so that the solvent and water in the membrane liquid can be exchanged thoroughly;
[0034] 2) In situ preparation of MOFs membrane: dissolve the organic ligand 2-ethylimidazole and the metal salt zinc hydroxide in the solvent methanol respectively, add concentrated ammonia water and mix evenly, and immerse the bottom membrane prepared in step 1) into the orga...
PUM
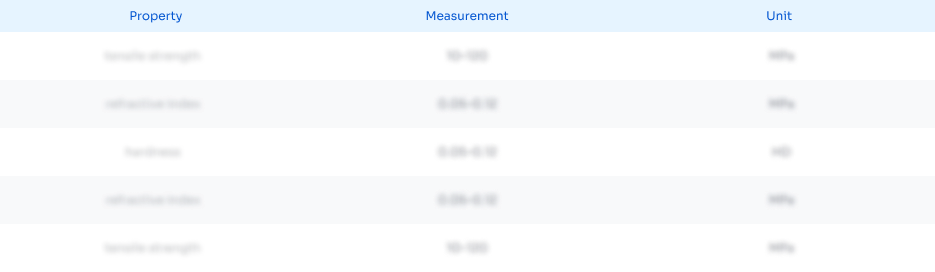
Abstract
Description
Claims
Application Information

- R&D Engineer
- R&D Manager
- IP Professional
- Industry Leading Data Capabilities
- Powerful AI technology
- Patent DNA Extraction
Browse by: Latest US Patents, China's latest patents, Technical Efficacy Thesaurus, Application Domain, Technology Topic, Popular Technical Reports.
© 2024 PatSnap. All rights reserved.Legal|Privacy policy|Modern Slavery Act Transparency Statement|Sitemap|About US| Contact US: help@patsnap.com