Preparation method of advanced oxidation system for treating oily sludge
An advanced oxidation and system technology, applied in the field of electrochemistry, can solve problems such as chemical stability and oxygen evolution overpotential difference
- Summary
- Abstract
- Description
- Claims
- Application Information
AI Technical Summary
Problems solved by technology
Method used
Image
Examples
Embodiment 1
[0033] This embodiment provides a method for preparing an advanced oxidation treatment oily sludge system, which is characterized in that it includes the following steps:
[0034] S1. Titanium substrate cleaning: Vacuum sintering is used to prepare a porous titanium plate 9 with a porosity of 20%. The porous titanium plate 9 is provided with a gas introduction cavity 10, and the porous titanium plate 9 is put into boiling degreasing liquid. After 1 hour, take it out and place it in deionized water and clean it with ultrasonic waves for 30 minutes; achieve the purpose of removing oil stains and oxide films on the surface, removing residual attachments in the pores of the porous titanium plate 9, and forming a pitted surface on the surface of the porous titanium plate 9.
[0035] S2. Etching: Put the porous titanium plate treated in step S1 into 10 wt% oxalic acid solution, heat to 100° C., keep it warm for 35 minutes, and rinse the porous titanium plate 9 with clean water after ...
Embodiment 2
[0042] This embodiment provides a method for preparing a titanium-based electrode containing a titanium oxide coating, comprising the following steps:
[0043] S1. Titanium substrate cleaning: Vacuum sintering is used to prepare a porous titanium plate 9 with a porosity of 10%. The porous titanium plate 9 is provided with a gas introduction cavity 10, and the porous titanium plate 9 is put into boiling degreasing liquid. After 2 hours, take it out and place it in deionized water and clean it with ultrasonic waves for 10 minutes; to achieve the purpose of removing oil stains and oxide films on the surface, removing residual attachments in the holes of the porous titanium plate 9, and forming a pitted surface on the surface of the porous titanium plate 9.
[0044] S2. Etching: Put the porous titanium plate 9 treated in step S1 into an 8wt% oxalic acid solution, heat it to 95° C., and keep it warm for 60 minutes. After the etching, rinse the porous titanium plate 9 with clean wate...
Embodiment 3
[0051] This embodiment provides a method for preparing a titanium-based electrode containing a titanium oxide coating, comprising the following steps:
[0052] S1. Titanium substrate cleaning: Vacuum sintering is used to prepare a porous titanium plate 9 with a porosity of 30%. The porous titanium plate 9 is provided with a gas introduction cavity 10, and the porous titanium plate 9 is put into boiling degreasing liquid. After 1 hour, take it out and place it in deionized water and clean it with ultrasonic waves for 20 minutes; achieve the purpose of removing oil stains and oxide films on the surface, removing residual attachments in the pores of the porous titanium plate 9, and forming a pitted surface on the surface of the porous titanium plate 9.
[0053] S2. Etching: put the porous titanium plate 9 treated in step S1 into a 10 wt% oxalic acid solution, heat to 100° C., and keep it warm for 30 minutes. After the etching, rinse the porous titanium plate 9 with clean water;
...
PUM
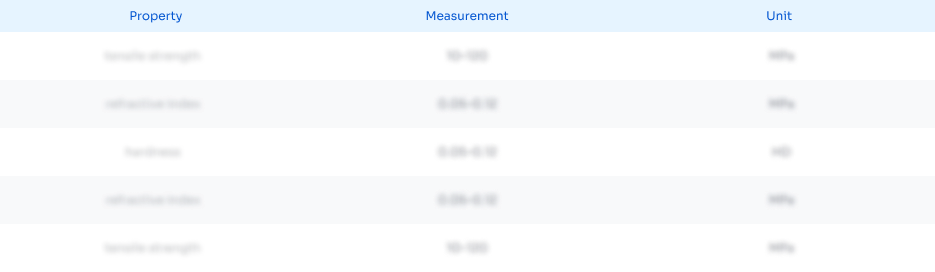
Abstract
Description
Claims
Application Information

- R&D
- Intellectual Property
- Life Sciences
- Materials
- Tech Scout
- Unparalleled Data Quality
- Higher Quality Content
- 60% Fewer Hallucinations
Browse by: Latest US Patents, China's latest patents, Technical Efficacy Thesaurus, Application Domain, Technology Topic, Popular Technical Reports.
© 2025 PatSnap. All rights reserved.Legal|Privacy policy|Modern Slavery Act Transparency Statement|Sitemap|About US| Contact US: help@patsnap.com