Low frequency torsional vibration reduction control system construction method based on hybrid drive
A hybrid drive and control system technology, applied to hybrid vehicles, control devices, motor vehicles, etc., can solve the problems of driver's driving comfort decline, output torque fluctuation, and system failure
- Summary
- Abstract
- Description
- Claims
- Application Information
AI Technical Summary
Problems solved by technology
Method used
Image
Examples
Embodiment
[0058] The power system of a plug-in hybrid electric vehicle is composed of an engine, a front transmission, two motors (A, B), a planetary coupling mechanism, a final reducer, a battery, a motor controller and other electrical components. The planetary coupling mechanism has a planetary row PG, Clutch and two brakes (Z1, Z2), the engine is connected to the front transmission of the vehicle, the output shaft of the front transmission is connected to the PG planet carrier, the motor A is connected to the PG sun gear and the brake Z1, the PG ring gear is connected to the brake Z2, and is connected to the brake Z2 through the clutch C1. Motor B is connected to the output shaft, and the output shaft transmits power to the drive shaft through the final reducer and differential to drive the vehicle; Moment T p is the coupling result of the output torque of the three power sources. Since the stiffness of the components of the coupling mechanism is much greater than that of the drive ...
PUM
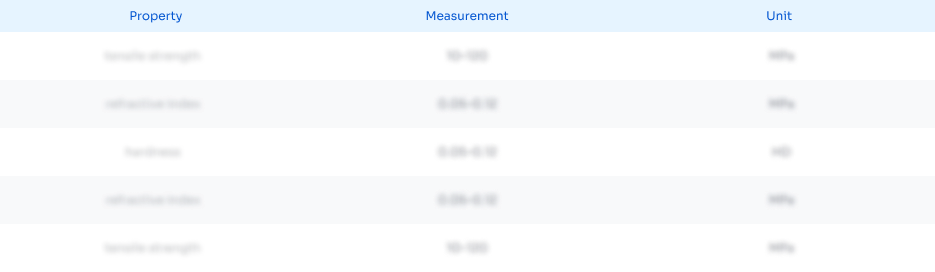
Abstract
Description
Claims
Application Information

- R&D
- Intellectual Property
- Life Sciences
- Materials
- Tech Scout
- Unparalleled Data Quality
- Higher Quality Content
- 60% Fewer Hallucinations
Browse by: Latest US Patents, China's latest patents, Technical Efficacy Thesaurus, Application Domain, Technology Topic, Popular Technical Reports.
© 2025 PatSnap. All rights reserved.Legal|Privacy policy|Modern Slavery Act Transparency Statement|Sitemap|About US| Contact US: help@patsnap.com