Transverse flux reciprocating motor and reciprocating compressor including the transverse flux reciprocating motor
A technology of reciprocating motor and transverse magnetic flux, applied in the field of reciprocating compressor and transverse magnetic flux reciprocating motor, can solve the problems of reducing motor size, unable to drive frequency, increasing power consumption, etc., to reduce friction loss and noise, and reduce manufacturing cost , the effect of improving work performance
- Summary
- Abstract
- Description
- Claims
- Application Information
AI Technical Summary
Problems solved by technology
Method used
Image
Examples
Embodiment Construction
[0073] The drawings of the following embodiments show embodiments with the same spirit, but in order to better understand the present invention, without departing from the spirit of the present invention, some parts may have different representations according to the drawings, and some parts may Not shown in the drawings, or some parts may be exaggerated according to the drawings.
[0074] figure 1 is a perspective view showing a transverse flux reciprocating motor according to an embodiment of the present invention. figure 2 Yes figure 1 A perspective view of the portion of the transverse flux shuttle motor shown.
[0075] like figure 1 and figure 2 As shown, the transverse flux flow reciprocating motor (hereinafter referred to as reciprocating motor for short) according to this embodiment may include a stator 100 , a magnet coil 210 , a magnet 300 and a mover 400 .
[0076] First of all, the stator 100 may include at least one of an inner stator 110 and an outer stato...
PUM
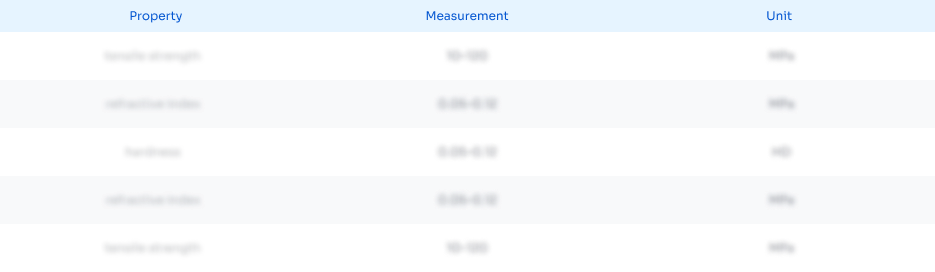
Abstract
Description
Claims
Application Information

- R&D Engineer
- R&D Manager
- IP Professional
- Industry Leading Data Capabilities
- Powerful AI technology
- Patent DNA Extraction
Browse by: Latest US Patents, China's latest patents, Technical Efficacy Thesaurus, Application Domain, Technology Topic, Popular Technical Reports.
© 2024 PatSnap. All rights reserved.Legal|Privacy policy|Modern Slavery Act Transparency Statement|Sitemap|About US| Contact US: help@patsnap.com