Aluminum alloy hot punching die provided with shape follow-up cooling water channels
A hot stamping die and conformal cooling technology, applied in the field of hot stamping dies, can solve the problems of difficult cooling and complex shapes of parts, and achieve the effects of easy processing, uniform performance and simple die structure
- Summary
- Abstract
- Description
- Claims
- Application Information
AI Technical Summary
Problems solved by technology
Method used
Image
Examples
Embodiment
[0027] Traditional hot stamping dies often use drilling to manufacture cooling channels, but this processing method can only produce straight-line cooling channels, which often results in uneven cooling for large and complex parts. In view of the above problems, the present invention provides a method for manufacturing a hot stamping die with a conformal cooling channel, which includes a mold main part, a mold surface part, a sealing ring, bolts, etc., and the mold main part and the mold surface part They need to be machined separately, and each has an accompanying semicircular hole. After the two are assembled together and fixed with bolts, they can form a complete mold cooling channel. The invention cleverly solves the problem that parts with complex shapes are difficult to cool after hot forming, and the conformal cooling water channel processed by this method can make the cooling speed of each part of the part more uniform, and the forming quality can be significantly impro...
PUM
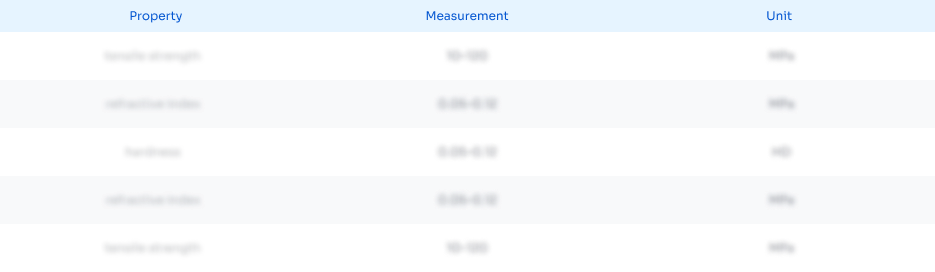
Abstract
Description
Claims
Application Information

- R&D
- Intellectual Property
- Life Sciences
- Materials
- Tech Scout
- Unparalleled Data Quality
- Higher Quality Content
- 60% Fewer Hallucinations
Browse by: Latest US Patents, China's latest patents, Technical Efficacy Thesaurus, Application Domain, Technology Topic, Popular Technical Reports.
© 2025 PatSnap. All rights reserved.Legal|Privacy policy|Modern Slavery Act Transparency Statement|Sitemap|About US| Contact US: help@patsnap.com