Improved nodular cast iron rail finishing roll and production method thereof
A production method and improved technology, applied in the direction of rolls, metal rolling, metal rolling, etc., can solve the problems affecting rolling efficiency and rolling precision, large hardness drop, roll failure, etc., to achieve easy promotion and use, The effect of reducing the hardness drop and prolonging the service life
- Summary
- Abstract
- Description
- Claims
- Application Information
AI Technical Summary
Problems solved by technology
Method used
Image
Examples
Embodiment 1
[0020] A production method of an improved nodular cast iron rail finishing roll, comprising the following steps: S1, optimizing the chemical composition: C: 3.20%; Si: 1.45%; Mn: 0.55%; P: 0.01%; S: 0.01%; Cr : 0.75%; Ni: 2.80%; Mo: 0.50%; V: 0.20%; Re: 0.05%; Mg: 0.05%; S: 0.01%; Ni: 2.30%; the rest is according to the requirements of finished products; the temperature of tap iron is controlled at 1410°C during spheroidizing treatment; NiMg spheroidizing agent 7kg / t+yttrium-based heavy rare earth 3kg / t is used; CaBa inoculant is used for inoculation treatment, Add Si3.5 kg / t in the bag and calm down for 8 minutes after inoculation; S3, during pouring, the temperature is controlled at 1290 °C; instantaneous inoculation during pouring, add Si0.5 kg / t, and quickly pour 5t / min; S4, after pouring After cooling to normal temperature, it is turned into a finished product by turning.
Embodiment 2
[0021] Embodiment 2: A production method of an improved nodular cast iron rail finishing roll, comprising the following steps: S1, optimizing the chemical composition: C: 3.30%; Si: 1.55%; Mn: 0.65%; P: 0.02%; S: 0.02%; Cr: 0.80%; Ni: 3.00%; Mo: 0.55%; V: 0.25%; Re: 0.10%; Mg: 0.06%; Ni: 0.02%; S: 0.02%; Ni: 2.35%; the rest is according to the requirements of finished products; the tapping temperature is controlled at 1420°C during spheroidizing treatment; NiMg spheroidizing agent 7kg / t+yttrium-based heavy rare earth 3.3 kg / t; inoculation treatment Use CaBa inoculant, add Si3.5 kg / t in the bag and calm down for 8 minutes after inoculation; S3, when pouring, the temperature is controlled at 1295 °C; instantaneous inoculation during pouring, add Si0.5 kg / t, and quickly pour 5t / min ; S4, after pouring and cooling to normal temperature, it is processed into finished product 2 by turning.
Embodiment 3
[0023] A production method of an improved nodular cast iron rail finishing roll, comprising the following steps: S1, optimizing the configuration chemical composition: C: 3.40%; Si: 1.65%; Mn: 0.75%; P: 0.03%; S: 0.025%; Cr : 0.85%; Ni: 3.20%; Mo: 0.60%; V: 0.30%; Re: 0.15%; Mg: 0.08%; S: 0.025%; Ni: 2.40%; the rest is according to the finished product requirements; the tap temperature is controlled at 1430°C during spheroidizing treatment; NiMg spheroidizing agent 7kg / t+yttrium-based heavy rare earth 3.5 kg / t is used; CaBa inoculant is used for inoculation treatment , add Si3.5 kg / t in the bag and sedate for 8 minutes after inoculation; S3, during pouring, the temperature is controlled at 1300 °C; instantaneous inoculation during pouring, add Si0.5 kg / t, rapid pouring 5t / min; S4, pouring Finally, after cooling to normal temperature, it is turned into a finished product through turning.
[0024] The finished products processed by the above-mentioned 3 production methods are t...
PUM
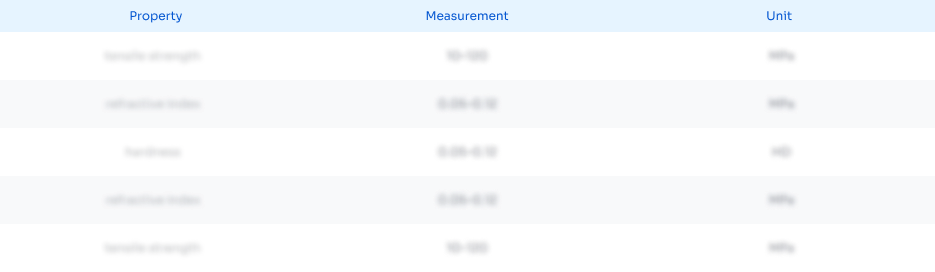
Abstract
Description
Claims
Application Information

- Generate Ideas
- Intellectual Property
- Life Sciences
- Materials
- Tech Scout
- Unparalleled Data Quality
- Higher Quality Content
- 60% Fewer Hallucinations
Browse by: Latest US Patents, China's latest patents, Technical Efficacy Thesaurus, Application Domain, Technology Topic, Popular Technical Reports.
© 2025 PatSnap. All rights reserved.Legal|Privacy policy|Modern Slavery Act Transparency Statement|Sitemap|About US| Contact US: help@patsnap.com