Preparation method and application of ZnO/CNF composite material
A technology of composite materials and polyvinyl alcohol, which is applied in chemical instruments and methods, rayon manufacturing, textiles and papermaking, etc., can solve the problems of high production cost, difficult industrialization, uneven dispersion, etc., and achieve continuous and stable production process. The product quality is stable and the effect of improving the degradation effect
- Summary
- Abstract
- Description
- Claims
- Application Information
AI Technical Summary
Problems solved by technology
Method used
Image
Examples
Embodiment 1
[0036] (1) Weigh 3.0152 g of polyvinyl alcohol (average molecular weight: 145,000) and dissolve it in 30 mL of distilled water, and stir evenly to obtain an aqueous solution of polyvinyl alcohol.
[0037] (2) Weigh 1.2390g of zinc acetate and pour it into the polyvinyl alcohol aqueous solution obtained in step (2), and stir at 80°C for 3 hours to obtain a spinning solution;
[0038] (3) Place the spinning solution obtained in step (2) in a syringe, perform electrospinning under the conditions of an electrospinning voltage of 15kV, a flow rate of 0.8mL / h and a receiving distance of 16cm, and dry at room temperature Overnight, ZnO / CNF precursor nanofibers were prepared.
[0039] (4) Place the ZnO / CNF precursor nanofibers obtained in step (3) in a porcelain boat, and 2 Under the condition of , gradually heating from room temperature to 600 ℃, calcined for 10.5h, the sample ZnO / CNF composite material was prepared.
[0040] The XRD figure of the ZnO / CNF precursor nanofiber prepar...
Embodiment 2
[0043] The difference between this embodiment and Example 1 is that the zinc acetate in step (2) is replaced by zinc nitrate, and the polyvinyl alcohol in step (1) and the zinc nitrate in step (2) are added according to the molar ratio of 1:400 , Electrospinning voltage is changed into 20kV in the step (3), and others are all the same as embodiment 1.
Embodiment 3
[0045] The difference between this embodiment and Example 1 is that the zinc acetate in the step (2) is replaced by zinc nitrate, and the polyvinyl alcohol in the step (1) and the zinc nitrate in the step (2) are added according to the molar ratio of 1:200 , the electrospinning flow rate in step (3) was changed to 1.0mL / h, and the calcination time in step (4) was 7h. Others are all the same as in Example 1.
PUM
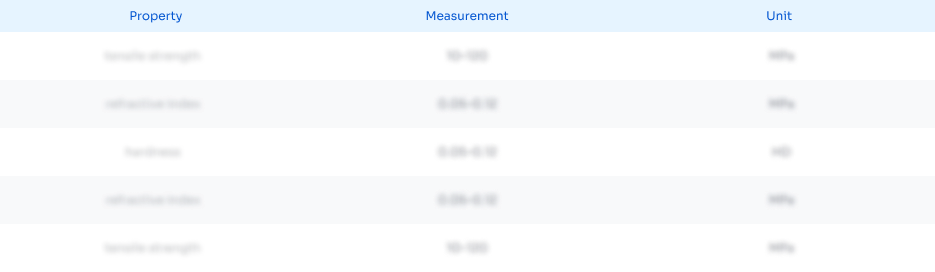
Abstract
Description
Claims
Application Information

- R&D
- Intellectual Property
- Life Sciences
- Materials
- Tech Scout
- Unparalleled Data Quality
- Higher Quality Content
- 60% Fewer Hallucinations
Browse by: Latest US Patents, China's latest patents, Technical Efficacy Thesaurus, Application Domain, Technology Topic, Popular Technical Reports.
© 2025 PatSnap. All rights reserved.Legal|Privacy policy|Modern Slavery Act Transparency Statement|Sitemap|About US| Contact US: help@patsnap.com