Bio-based flame-retardant furan epoxy resin and preparation method thereof
A technology of furan epoxy resin and deoxyfuran epoxy resin, which is applied in the field of bio-based flame-retardant furan epoxy resin and its preparation, can solve the problems of easy generation of toxic gas and relatively few studies on flame retardancy, and achieve the goal of realizing Efficient utilization, strong substitutability, and high biological safety
- Summary
- Abstract
- Description
- Claims
- Application Information
AI Technical Summary
Problems solved by technology
Method used
Image
Examples
Embodiment 1
[0054] Weigh furan epoxy resin BOF (2.4g, 10mmol) in the reaction bottle, pass into nitrogen, after removing the oxygen component, under nitrogen atmosphere, add 4,4'-diaminodiphenyl sulfone (44DDS, 1.2g, 5mmol ) to further remove the air, fully mix and stir, and heat up to 140°C to melt and mix them evenly. The material was uniformly poured into a stainless steel mold plate, and the mold plate was moved into a nitrogen curing box at 185° C., cured for 3 hours, and then cooled naturally under a nitrogen atmosphere to obtain a yellow transparent epoxy resin polymer (crosslinking density: 2.38mol / dm 3 ). Micro Combustion Calorimetry (MCC) experimental results show a maximum heat release rate of 175W / g ( Figure 8 ). The characteristic infrared absorption peak of the prepared bio-based flame-retardant furan epoxy resin: 681cm -1 (δ, C-H, Ar), 786cm -1 (δ, C-H, Ar), 1095cm -1 (vs, C-O-C, ether), 1200cm -1 (vs, C-O-C, furan), 1282cm -1 (v as , C-O-C, ether), 1354cm -1 (v...
Embodiment 2
[0056] Weigh furan epoxy resin OmbFdE (3.5g, 10mmol) in the reaction flask, pass into nitrogen, after removing the oxygen component, under nitrogen atmosphere, add 4,4'-diaminodiphenyl sulfone (44DDS, 1.2g, 5mmol ) to further remove the air, fully mix and stir, and heat up to 130°C to melt the two and mix evenly. The material was uniformly poured into a stainless steel mold plate, and the mold plate was moved into a nitrogen curing box at 175° C., cured for 4 hours, and then cooled naturally under a nitrogen atmosphere to obtain a yellow opaque epoxy resin polymer (crosslinking density: 2.16mol / dm 3 ). Micro-combustion calorimetry (MCC) experiment results show that the maximum heat release rate is 223W / g.
Embodiment 3
[0058] Weigh furan epoxy resin BOF (2.4g, 10mmol) in the reaction bottle, pass into nitrogen, after removing the oxygen component, under nitrogen atmosphere, add 3,3'-diaminodiphenyl sulfone (33DDS, 1.2g, 5mmol ) to further remove the air, fully mix and stir, and heat up to 130°C to melt the two and mix evenly. The material was uniformly poured into a stainless steel mold plate, and the mold plate was moved into a nitrogen curing box at 170° C., solidified for 3 hours, and then cooled naturally under a nitrogen atmosphere to obtain a yellow transparent epoxy resin polymer (crosslinking density: 3.62 mol / dm 3 ). Micro Combustion Calorimetry (MCC) experiment results show that the maximum heat release rate is 112W / g ( Figure 8 ). The characteristic infrared absorption peak of the prepared bio-based flame-retardant furan epoxy resin: 690cm -1 (δ, C-H, Ar), 786cm -1 (δ, C-H, Ar), 1070cm -1 (vs, C-O-C, ether), 1208cm -1 (vs, C-O-C, furan), 1290cm -1 (vas, C-O-C, ether), 13...
PUM
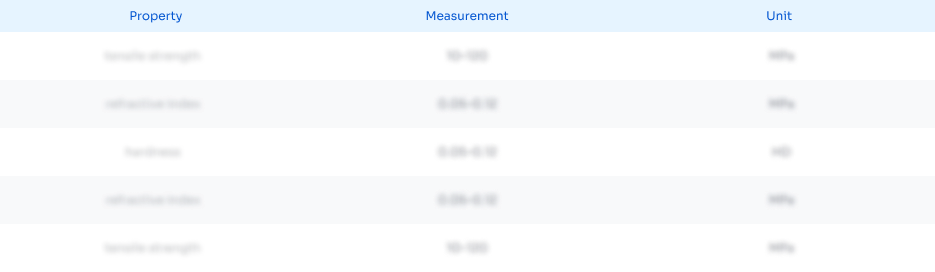
Abstract
Description
Claims
Application Information

- R&D
- Intellectual Property
- Life Sciences
- Materials
- Tech Scout
- Unparalleled Data Quality
- Higher Quality Content
- 60% Fewer Hallucinations
Browse by: Latest US Patents, China's latest patents, Technical Efficacy Thesaurus, Application Domain, Technology Topic, Popular Technical Reports.
© 2025 PatSnap. All rights reserved.Legal|Privacy policy|Modern Slavery Act Transparency Statement|Sitemap|About US| Contact US: help@patsnap.com